Coke making coal blending method with black-jack participated
A coking coal and lean coal technology, applied in coking ovens, petroleum industry, etc., can solve the problems of less cracks, poor coking performance, and low volatile content
- Summary
- Abstract
- Description
- Claims
- Application Information
AI Technical Summary
Problems solved by technology
Method used
Examples
Embodiment 1
[0031] The coking coal used in this embodiment 1 is domestic coal, and the raw coal property analysis is as follows:
[0032] Single coal sample Ash % Volatile % Sulfur % G Y R max R max <1.35% ratio
[0033] Gas fertilizer coal 8.19 42.34 1.70 97 27 0.65 100
[0034] 1 / 3 coking coal 9.23 33.93 0.65 77 14.5 0.85 100
[0035] Coking coal 10.29 24.68 0.45 87 17 1.28 74
[0036] Lean coal 10.89 16.48 0.40 48 6 1.45 48
[0037] For lean coal that participates in coal blending, its vitrinite reflectance R max <1.35% specific interval ratio is 48%, lean coal is the first sub-category lean coal.
[0038] The coal blending scheme of the present embodiment 1 is: gas fat coal: 8%; 1 / 3 coking coal: 38%; coking coal: 37%; lean coal: 17%.
[0039] Coke the obtained coal blend in a 6-meter coke oven, and the quality of the obtained coke is: crushing strength M40: 82.1%; wear resistance M10: 6.72%; reactivity (CRI): 27.9%, post-reaction strength (CSR): 65.8% . qualified.
Embodiment 2
[0041] The coking coal used in this embodiment 2 is domestic coal, and the raw coal property analysis is as follows:
[0042] Single coal sample Ash % Volatile % Sulfur % G Y R max R max <1.35-1.70% ratio
[0043] Gas fertilizer coal 8.24 43.12 1.68 95 26 0.63 0
[0044] 1 / 3 coking coal 9.52 34.26 0.61 74 13.5 0.89 0
[0045] Fatty coal 9.54 32.86 0.98 89 27 0.98 0
[0046] Coking coal 10.12 23.88 0.47 79 16.5 1.18 12
[0047] Lean coal 9.98 16.64 0.43 38 6 1.62 76
[0048] For lean coal that participates in coal blending, its vitrinite reflectance R max The specific interval ratio of 1.35-1.70% is 76%, lean coal is the second sub-category lean coal.
[0049] The coal blending scheme of Example 2 is: gas fat coal: 5%; 1 / 3 coking coal: 39%; fat coal: 5%; coking coal: 36%; lean coal: 15%.
[0050] Coke the obtained coal blend in a 4.63-meter coke oven, and the quality of the obtained coke is: crushing strength M 40 : 80.21%, abrasion resistance M 10 : 6.88%, reacti...
Embodiment 3
[0052] The coking coal used in this embodiment 3 is domestic coal, and the raw coal property analysis is as follows:
[0053] Single coal sample Ash % Volatile % Sulfur % G Y R max R max >1.70% ratio
[0054] Gas coal 8.24 38.12 0.56 56 10 0.63 0
[0055] 1 / 3 coking coal 9.52 34.26 0.61 74 13.5 0.89 0
[0056] Fatty coal 9.54 32.86 0.98 89 27 0.98 0
[0057]Coking coal 10.12 23.88 0.47 79 16.5 1.18 0
[0058] Lean coal 9.98 16.64 0.43 38 6 1.62 76
[0059] For lean coal that participates in coal blending, its vitrinite reflectance R max The proportion of specific interval >1.70% is 76%, and the lean coal is the third sub-category lean coal.
[0060] The coal blending scheme of Example 3 is: gas coal: 5%; 1 / 3 coking coal: 38%; fat coal: 8%; coking coal: 39%; lean coal: 10%.
[0061] Coke the obtained coal blend in a 4.63-meter coke oven, and the quality of the obtained coke is: crushing strength M 40 : 80.98%, abrasion resistance M 10 : 6.72%, reactivity (CRI): 29...
PUM
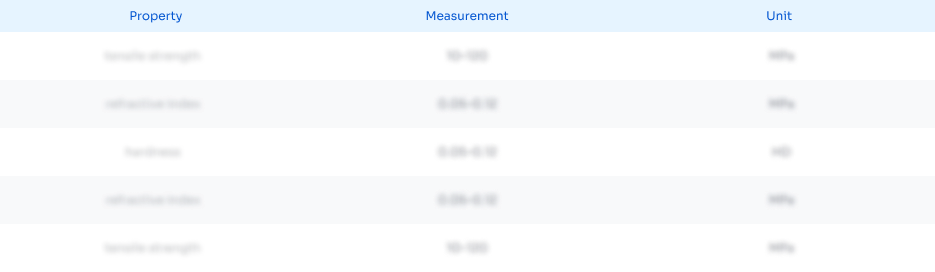
Abstract
Description
Claims
Application Information

- R&D
- Intellectual Property
- Life Sciences
- Materials
- Tech Scout
- Unparalleled Data Quality
- Higher Quality Content
- 60% Fewer Hallucinations
Browse by: Latest US Patents, China's latest patents, Technical Efficacy Thesaurus, Application Domain, Technology Topic, Popular Technical Reports.
© 2025 PatSnap. All rights reserved.Legal|Privacy policy|Modern Slavery Act Transparency Statement|Sitemap|About US| Contact US: help@patsnap.com