Vibrating-type motor
A motor and vibration technology, applied in the direction of electrical components, electromechanical devices, etc., can solve the problems that the piston and the cylinder cannot be supported in a non-contact manner, and the structure is heavy, and achieve the effect of light weight, low price and small size
- Summary
- Abstract
- Description
- Claims
- Application Information
AI Technical Summary
Problems solved by technology
Method used
Image
Examples
Embodiment Construction
[0037] FIG. 1 is a schematic diagram showing a vibration motor according to the present invention. As discussed above with regard to FIGS. 6 to 9 , FIG. 1 shows a portion of a section taken along the central axis C of a substantially cylindrical motor. FIG. 1 shows a motor, which includes a field yoke 1 , a field coil 2 wound on the field yoke 1 , a back yoke 3 and a moving part 4 . The moving part 4 is formed by a permanent magnet arranged in a yoke gap portion between the field yoke 1 and the back yoke 3 . A conventional frame for supporting the moving part 4 is not shown in the figures.
[0038] As shown in FIG. 1, the moving part 4 is constructed by coaxially and integrally connecting the auxiliary magnets 6 and 7 at connection positions 8, 9 to the two-axis ends of the main magnet 5, wherein the main magnet 5 has its outer circumferential side as N pole and its inner circumference side is S pole. The auxiliary magnets 6 and 7 are magnetized in the opposite direction to...
PUM
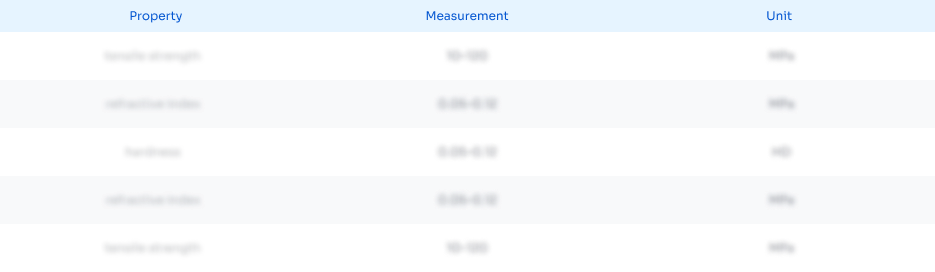
Abstract
Description
Claims
Application Information

- R&D Engineer
- R&D Manager
- IP Professional
- Industry Leading Data Capabilities
- Powerful AI technology
- Patent DNA Extraction
Browse by: Latest US Patents, China's latest patents, Technical Efficacy Thesaurus, Application Domain, Technology Topic, Popular Technical Reports.
© 2024 PatSnap. All rights reserved.Legal|Privacy policy|Modern Slavery Act Transparency Statement|Sitemap|About US| Contact US: help@patsnap.com