Method for pressing tank-type bulkhead using three rollers rolling machine
A technology for pressing grooves and triggers, which is used in forming tools, manufacturing tools, metal processing equipment, etc., and can solve the problems of large pressing workload and splicing workload, long production cycle of ship trough bulkheads, and unsmooth butt joints, etc. problems, to achieve the effect of reducing the workload of pressing and splicing, reducing the number of vertical splicing, and speeding up the production cycle
- Summary
- Abstract
- Description
- Claims
- Application Information
AI Technical Summary
Problems solved by technology
Method used
Image
Examples
Embodiment Construction
[0026] see figure 1 , the present invention discloses a method of using a three-roll plate rolling machine to press a grooved bulkhead during shipbuilding, the method comprising:
[0027] According to the diameter of the upper and lower rollers of the three-roller plate bending machine and the gap between the two lower rollers, the upper mold base 2.1 and the lower mold base 3.2 of the upper and lower molds of the mold and the rollers are designed; it is determined according to the effective working length of the three-roller plate bending machine The length of the mould; according to the size of the knuckle of the notch of the grooved bulkhead and the arc at the knuckle, the size of the upper die pressure head and the lower die groove 3.1 of the upper and lower dies is designed.
[0028] Connect and fix the upper mold and the upper roller 1 through the screw buckle, place the lower mold on the two lower rollers, and then drive the upper mold to run downward through the upper ...
PUM
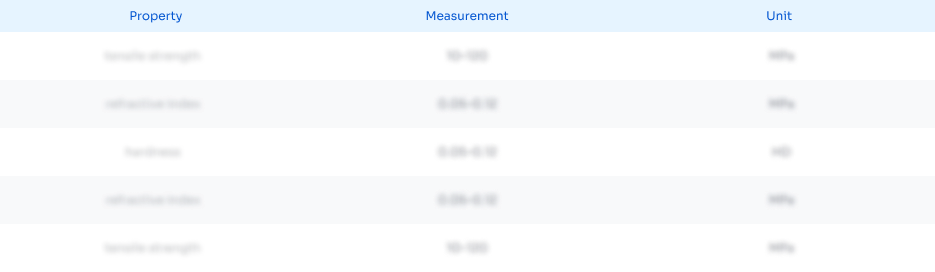
Abstract
Description
Claims
Application Information

- R&D
- Intellectual Property
- Life Sciences
- Materials
- Tech Scout
- Unparalleled Data Quality
- Higher Quality Content
- 60% Fewer Hallucinations
Browse by: Latest US Patents, China's latest patents, Technical Efficacy Thesaurus, Application Domain, Technology Topic, Popular Technical Reports.
© 2025 PatSnap. All rights reserved.Legal|Privacy policy|Modern Slavery Act Transparency Statement|Sitemap|About US| Contact US: help@patsnap.com