Contact lenses plastics mould used for semi-lathe production and manufacturing method thereof
A technology for contact lenses and plastic molds, which is applied to household appliances, other household appliances, applications, etc., can solve the problem of easy separation of polymer blanks from male molds and internal stress of contact lenses, and achieve the effect of uncomplicated preparation process.
- Summary
- Abstract
- Description
- Claims
- Application Information
AI Technical Summary
Problems solved by technology
Method used
Image
Examples
Embodiment 1
[0029] The preparation method of the contact lens plastic mold that is used for semi-turning method production comprises following steps and technological condition:
[0030] (1) Preparation of the male mold core: electroplate metal nickel on the carbon steel, and obtain a contact lens male mold core (core) with 2 arcs and multi-curved surfaces after precision machining. Specifically, the electroplating thickness is about 0.3mm on a carbon steel blank with a reserved radius (R)=8, sagittal height (h)=3mm concave surface, outer diameter (ф)=12.5mm, length (L)=20mm The metal nickel is then placed on a precision CNC lathe (such as the OPTOFORM 80A of Sterling Ultra Precision Inc.) to turn a metal mold core with 4 arc-curved surfaces. The curved surface formed by the first arc corresponds to the inner optical zone of the lens, and the positions of the second to fourth arcs are the transition zone between the optical zone and the edge, with a width of 0.55mm. The schematic diagram...
Embodiment 2
[0052] (1) Preparation of the male mold core: electroplate metal nickel on the carbon steel, and obtain a contact lens male mold core (core) with 2 arcs and multi-curved surfaces after precision machining. Specifically, the electroplating thickness is about 0.3mm on a carbon steel blank with a reserved radius (R)=8, sagittal height (h)=3mm concave surface, outer diameter (ф)=12.5mm, length (L)=20mm The metal nickel is then placed on a precision CNC lathe (such as the OPTOFORM 80A of Sterling Ultra Precision Inc.) to turn a metal mold core with 4 arc-curved surfaces. The curved surface formed by the first arc corresponds to the inner optical zone of the lens, and the positions of the second to fourth arcs are the transition zone between the optical zone and the edge, with a width of 0.55mm. The schematic diagram of the appearance of the metal mold core is shown in Figure 1a and Figure 1b, which are the arc segment R1 with a radius of 7.260mm, the arc segment R2 with a radius of...
Embodiment 3
[0074] (1) Preparation of the male mold core: electroplate metal nickel on the carbon steel, and obtain a contact lens male mold core (core) with 2 arcs and multi-curved surfaces after precision machining. Specifically, metal nickel with a thickness of about 0.3mm is electroplated on a carbon steel blank with a reserved radius R=8, sagittal height h=3mm concave surface, outer diameter ф=12.5mm, and length L=20mm, and then placed On a precision CNC lathe (OPTOFORM 80A of Sterling Ultra Precision Inc.), a metal mold core with 4 arc-curved surfaces was turned. The curved surface formed by the first arc corresponds to the inner optical zone of the lens, and the positions of the second to fourth arcs are the transition zone between the optical zone and the edge, with a width of 0.55mm. The schematic diagram of the appearance of the metal mold core is shown in Figure 1a and Figure 1b, which are the arc segment R1 with a radius of 7.260mm, the arc segment R2 with a radius of 7.433mm,...
PUM
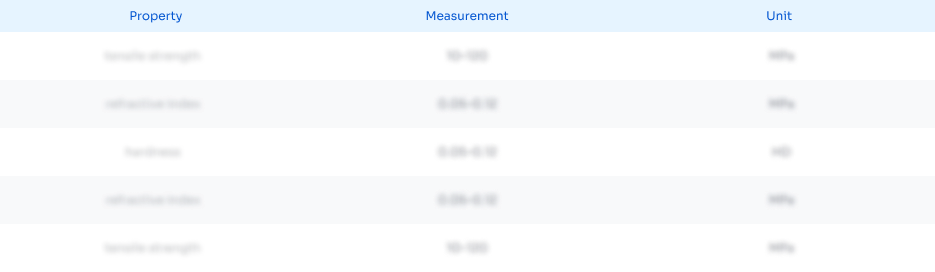
Abstract
Description
Claims
Application Information

- R&D Engineer
- R&D Manager
- IP Professional
- Industry Leading Data Capabilities
- Powerful AI technology
- Patent DNA Extraction
Browse by: Latest US Patents, China's latest patents, Technical Efficacy Thesaurus, Application Domain, Technology Topic, Popular Technical Reports.
© 2024 PatSnap. All rights reserved.Legal|Privacy policy|Modern Slavery Act Transparency Statement|Sitemap|About US| Contact US: help@patsnap.com