Blaze-folding corner structure for weakening furnace outlet remainder rotation
A furnace exit and refraction angle technology, applied in the field of refraction angle structure, can solve problems such as drop, adverse effects of pulverized coal, and influence on boiler combustion stability, so as to reduce the flow area, strengthen the racemization effect, and increase the flue gas flow rate Effect
- Summary
- Abstract
- Description
- Claims
- Application Information
AI Technical Summary
Problems solved by technology
Method used
Image
Examples
Embodiment 1
[0018] Embodiment 1: Referring to Figure 2, this embodiment retains the traditional flame bending angle for the rear wall, and bends the water-cooled wall tube of the front wall opposite to the rear wall to form a triangular or trapezoidal flame bending angle 1 to form a flame bending angle The water wall tubes in corner 1 are divided into n (n≥1) groups, and each group has at least two water wall tubes. The water-cooled wall tubes inside each group are bent in turn from right to left, and the depth of insertion into the furnace increases sequentially to form alternate staggered tube rows.
Embodiment 2
[0019] Embodiment 2, referring to Fig. 3, in this embodiment, the water-cooled wall tubes on the front and rear furnace walls are all bent to form a triangular or trapezoidal folded flame angle 1, and the water-cooled wall tubes forming the flame folded angle 1 are divided into n(n ≥1) group, each group of water wall tubes shall be at least two. The water-cooled wall tubes inside each group are bent in turn from right to left, and the depth of insertion into the furnace increases sequentially to form alternate staggered tube rows. The water-cooled wall tube rows forming the flame angle on the front and back furnace walls are symmetrically distributed.
Embodiment 3
[0020] Embodiment 3, referring to Fig. 4, in this embodiment, the water-cooled wall tubes on the front and rear walls of the furnace are all bent to form a triangular or trapezoidal folded flame angle 1, and the water-cooled wall tubes forming the folded flame angle 1 are divided into n( n≥1) groups, each group has at least two water wall tubes. Bend the water-cooled wall tubes inside each group of the front wall from right to left, and the depth of insertion into the furnace increases sequentially to form alternately staggered tube rows; bend the water-cooled wall tubes inside each group of the rear wall from left to right Bending, the depth of insertion into the furnace increases sequentially, forming alternately staggered tube rows. The water-cooled wall tube rows forming the flame angle on the front and rear walls of the furnace are in the form of staggered and symmetrical distribution.
PUM
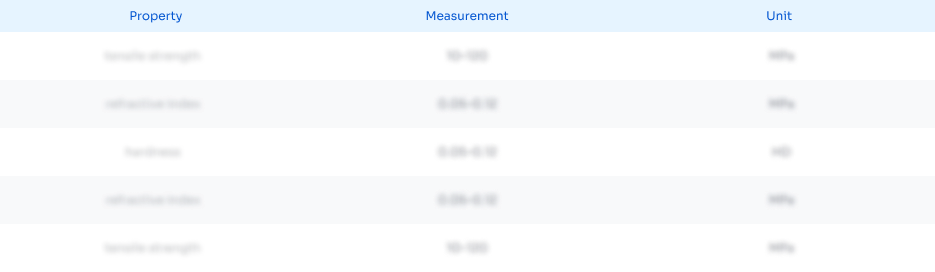
Abstract
Description
Claims
Application Information

- R&D
- Intellectual Property
- Life Sciences
- Materials
- Tech Scout
- Unparalleled Data Quality
- Higher Quality Content
- 60% Fewer Hallucinations
Browse by: Latest US Patents, China's latest patents, Technical Efficacy Thesaurus, Application Domain, Technology Topic, Popular Technical Reports.
© 2025 PatSnap. All rights reserved.Legal|Privacy policy|Modern Slavery Act Transparency Statement|Sitemap|About US| Contact US: help@patsnap.com