Ultrathin glass cleaning carrying robot
A technology for handling robots and ultra-thin glass. It is applied in the directions of manipulators, conveyor objects, transportation and packaging, etc. It can solve the problems of not meeting the production cycle requirements of ultra-thin glass, low production efficiency of thick glass handling equipment, and high glass fragmentation rate. Achieve the effect of fast production tempo, easy high-speed movement and simple process
- Summary
- Abstract
- Description
- Claims
- Application Information
AI Technical Summary
Problems solved by technology
Method used
Image
Examples
Embodiment Construction
[0022] Such as figure 2 As shown, the present invention adopts two groups of frame-type columns 1 structures as the fixing and support of the whole equipment, and the span between the two groups of frame-type columns 1 is 8.8 meters. Both ends of the beam assembly 2 are respectively connected with two sets of frame columns 1 by means of bolt connection. The beam assembly 2 is welded by two rectangular square steel pipes, and reinforced by welding steel plates on the upper and lower surfaces of the rectangular square steel pipes. An X guide rail 4 is installed on the beam assembly 2, and a support 8 is installed on the X guide rail 4. The support 8 is a welded frame structure, and the X guide rail 4 is slidably connected with the support 8. One end of the X synchronous toothed belt 5 is connected to one end of the mounting plate of the bracket 8, and the other end of the X synchronous toothed belt 5 bypasses the driving synchronous belt pulley 14 and the driven synchronous bel...
PUM
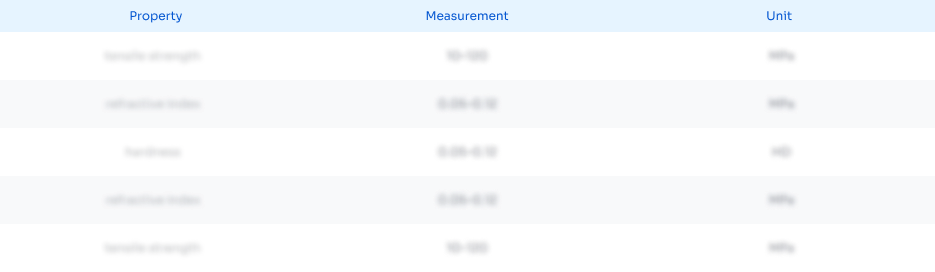
Abstract
Description
Claims
Application Information

- R&D
- Intellectual Property
- Life Sciences
- Materials
- Tech Scout
- Unparalleled Data Quality
- Higher Quality Content
- 60% Fewer Hallucinations
Browse by: Latest US Patents, China's latest patents, Technical Efficacy Thesaurus, Application Domain, Technology Topic, Popular Technical Reports.
© 2025 PatSnap. All rights reserved.Legal|Privacy policy|Modern Slavery Act Transparency Statement|Sitemap|About US| Contact US: help@patsnap.com