Method for circulating utilization of reclaimed pyrolusite powder in benzoquinone manufacturing technique
A technology of pyrolusite powder and production process, which is applied in the field of recycling pyrolusite powder in the production process of p-benzoquinone, can solve the problems of high consumption of manganese powder, different particle sizes, and the impact of benzoquinone yield, etc., and achieve an increase Utilization rate, the effect of obvious economic benefits
- Summary
- Abstract
- Description
- Claims
- Application Information
AI Technical Summary
Problems solved by technology
Method used
Image
Examples
Embodiment 1
[0009] Example 1: In a 2L reactor, 600g of pyrolusite powder with a manganese dioxide content of 45%, 1350ml of 36% dilute sulfuric acid were added, and 120g of aniline was added dropwise. After the reaction was completed, p-benzoquinone was distilled out, crystallized, and dried to obtain p-benzoquinone Quinone 95g, the distillation residue is separated waste liquid and manganese slag through gravity settling, and manganese slag is about 400g, and analysis manganese dioxide content is 5%, waste liquid is processed into manganese product, obtains manganese sulfate product 320g. In another 2L reactor, add 600g of pyrolusite powder with manganese dioxide content of 45%, 400g of recovered manganese powder, 1350ml of 36% dilute sulfuric acid, and dropwise add 120g of aniline. After the reaction is completed, p-benzoquinone is distilled out, crystallized and dried. 98g of p-benzoquinone was obtained, and the distillation residue was separated by gravity sedimentation into waste liqu...
Embodiment 2
[0010] Example 2: In a 2L reactor, 600g of pyrolusite powder with a manganese dioxide content of 70%, 1350ml of 36% dilute sulfuric acid were added, and 120g of aniline was added dropwise. After the reaction was completed, p-benzoquinone was distilled out, crystallized, and dried to obtain p-benzoquinone Quinone 105g, the distillation residue is separated waste liquid and manganese slag through gravity settling, and manganese slag is about 360g, and analysis manganese dioxide content is 40%, and waste liquid is processed into manganese product, obtains manganese sulfate product 378g. In another 2L reactor, add 600g of pyrolusite powder with manganese dioxide content of 70%, 360g of recovered manganese powder, 1350ml of 36% dilute sulfuric acid, and dropwise add 120g of aniline. After the reaction is completed, p-benzoquinone is distilled out, crystallized and dried. 113g of p-benzoquinone was obtained, and the distillation residue was separated by gravity sedimentation into was...
PUM
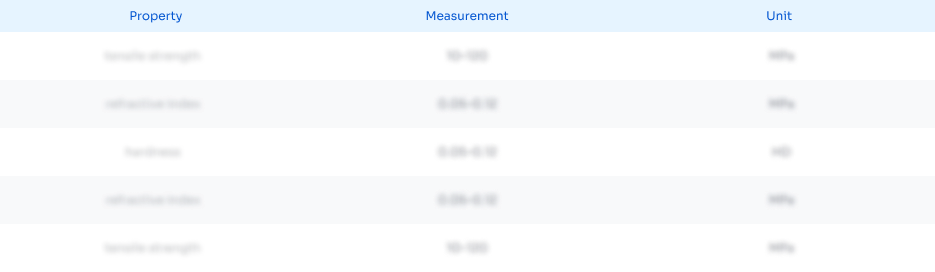
Abstract
Description
Claims
Application Information

- R&D
- Intellectual Property
- Life Sciences
- Materials
- Tech Scout
- Unparalleled Data Quality
- Higher Quality Content
- 60% Fewer Hallucinations
Browse by: Latest US Patents, China's latest patents, Technical Efficacy Thesaurus, Application Domain, Technology Topic, Popular Technical Reports.
© 2025 PatSnap. All rights reserved.Legal|Privacy policy|Modern Slavery Act Transparency Statement|Sitemap|About US| Contact US: help@patsnap.com