Angular rate sensor
An angular velocity sensor and angular velocity technology, applied in the direction of measuring acceleration, gyro effect for speed measurement, instruments, etc., can solve problems such as noise, separation, and unintended vibration, and achieve the effects of improving sensitivity, reducing noise, and high sensitivity
- Summary
- Abstract
- Description
- Claims
- Application Information
AI Technical Summary
Problems solved by technology
Method used
Image
Examples
Embodiment Construction
[0029] Several embodiments of the present invention are described below with the accompanying drawings. In the drawings of the respective embodiments, the same symbols represent the same components or equivalent components.
[0030] An angular velocity sensor according to a first embodiment of the present invention will be described with reference to FIGS. 1 to 3 . FIG. 1 shows a schematic cross-sectional view of this embodiment, and FIG. 2 shows a schematic plan view of an element substrate of this embodiment.
[0031] As shown in FIG. 1 , an angular velocity sensor 1 of this embodiment is composed of three layers of a support substrate 2 , an element substrate 3 , and a wiring substrate 4 . The movable part of the sensor is formed in the element substrate 3 , and the structure of the element substrate 3 includes a part engaged and fixed with the support substrate 2 and a part separated from the support substrate 2 and displaceably supported in the element substrate 3 .
[...
PUM
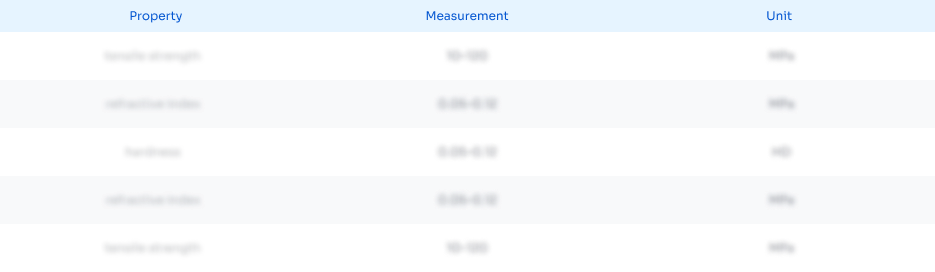
Abstract
Description
Claims
Application Information

- R&D Engineer
- R&D Manager
- IP Professional
- Industry Leading Data Capabilities
- Powerful AI technology
- Patent DNA Extraction
Browse by: Latest US Patents, China's latest patents, Technical Efficacy Thesaurus, Application Domain, Technology Topic, Popular Technical Reports.
© 2024 PatSnap. All rights reserved.Legal|Privacy policy|Modern Slavery Act Transparency Statement|Sitemap|About US| Contact US: help@patsnap.com