Multi-piece part composed of metal element and manufacturing method thereof
A technology of metal components and components, applied in the field of welding equipment, can solve problems such as loss of toughness and embrittlement, achieve low welding internal stress, reliable mutual docking, and prevent aging
- Summary
- Abstract
- Description
- Claims
- Application Information
AI Technical Summary
Problems solved by technology
Method used
Image
Examples
Embodiment Construction
[0069] Firstly, it is provided that the same parts of the different embodiments of the description are provided with the same designation or the same component designation, wherein the disclosure content contained in the entire description can be transferred to the same parts with the same designation or the same component designation . Also selected positional indications in the description, such as top, bottom, side, etc., refer to the directly described and illustrated figure and, when the position is changed, are automatically transferred to the new position. Furthermore, individual features or combinations of features from the various exemplary embodiments shown and described also constitute independent inventions or solutions according to the invention. It should also be pointed out in this connection that only the curved edges forming the deformation region 18 are shown schematically.
[0070] Different views of a first embodiment of the component 1 according to the in...
PUM
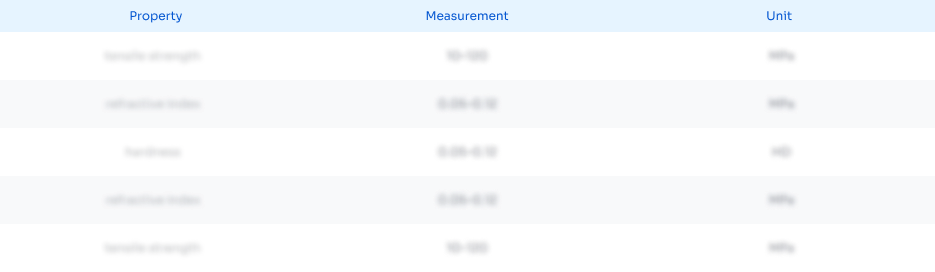
Abstract
Description
Claims
Application Information

- R&D
- Intellectual Property
- Life Sciences
- Materials
- Tech Scout
- Unparalleled Data Quality
- Higher Quality Content
- 60% Fewer Hallucinations
Browse by: Latest US Patents, China's latest patents, Technical Efficacy Thesaurus, Application Domain, Technology Topic, Popular Technical Reports.
© 2025 PatSnap. All rights reserved.Legal|Privacy policy|Modern Slavery Act Transparency Statement|Sitemap|About US| Contact US: help@patsnap.com