Auxiliary fractional tower and its gasoline catalyzing and olefine reducing modification process
A technology of fractionation tower and naphtha, which is applied in the fields of hydrocarbon distillation and petroleum industry, etc. It can solve the problems of unutilized top circulation heat at the appropriate temperature, increase the cooling load of the system, and downgrade the use of heat, so as to improve the distribution of reaction products and increase the The effect of heat exchange final temperature and reduction of production amount
- Summary
- Abstract
- Description
- Claims
- Application Information
AI Technical Summary
Problems solved by technology
Method used
Image
Examples
Embodiment 1
[0043] Such as Figure 4 As shown, the auxiliary fractionation tower of the present invention includes a tower body 1, and 16 trays are installed in the tower body 1 horizontally from top to bottom, and the whole tower body 1 is divided into 17 layers, the 17th layer It is a washing section, and a herringbone baffle 12 is installed in the vertical direction of this section, and the lower tower body of the herringbone baffle 12 is respectively provided with a reaction oil gas feed port 9, a stirring steam feed port 10, and a herringbone baffle 12. The upper tower body is provided with an oil slurry inlet 11 (externally connected to the main fractionation tower), and the bottom of the tower body 1 is provided with an oil slurry outlet 34, which is connected with the main fractionation tower through the oil slurry extraction pump 31 and the oil slurry heat exchanger 48 , the tray of the 16th tray 1-16 is provided with a middle section and a diesel outlet 4, and the 13th tray 1-13...
Embodiment 2
[0065] The feed temperature of the high-temperature reaction oil gas in the first step is 400°C, and the feed pressure is 0.20MPa; A part of the bottom of the liquid tank is pumped out directly to the absorption stabilization system, and the rich gas at 30°C is pumped out from the top of the liquid separation tank to also directly go to the absorption stabilization system. The oil and gas output pressure at the top of the tower is 0.16MPa; The return temperature is 80°C to ensure the heat balance of the whole tower; the return temperature of the middle section of the reflux controlled in the fourth step is 170°C to ensure the heat balance of the whole tower; all the other conditions are the same as in Embodiment 1.
Embodiment 3
[0067] The feed temperature of the high-temperature reaction oil gas in the first step is 450°C, and the feed pressure is 0.23MPa; A part is pumped out from the bottom of the liquid tank to directly absorb and stabilize the system, and the rich gas at 35°C is pumped out from the top of the liquid separation tank to directly absorb and stabilize the system. The oil and gas output pressure at the top of the tower body is 0.22MPa; The return temperature is 100° C. to ensure the heat balance of the entire tower; the fourth step controls the return temperature of the mid-section reflux to be 190° C. to ensure the heat balance of the entire tower; the remaining conditions are the same as in Embodiment 1.
PUM
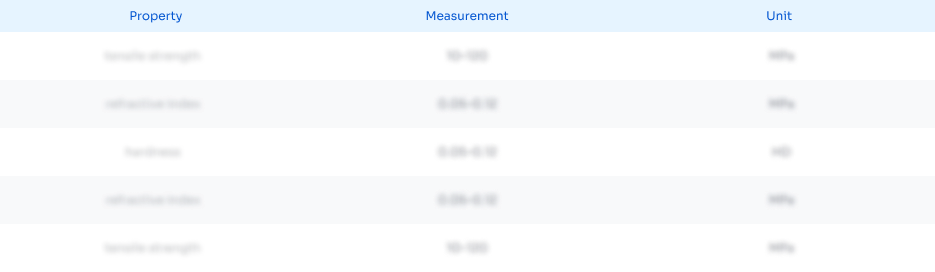
Abstract
Description
Claims
Application Information

- R&D
- Intellectual Property
- Life Sciences
- Materials
- Tech Scout
- Unparalleled Data Quality
- Higher Quality Content
- 60% Fewer Hallucinations
Browse by: Latest US Patents, China's latest patents, Technical Efficacy Thesaurus, Application Domain, Technology Topic, Popular Technical Reports.
© 2025 PatSnap. All rights reserved.Legal|Privacy policy|Modern Slavery Act Transparency Statement|Sitemap|About US| Contact US: help@patsnap.com