Intermeshing element mixer
A technology of mixers and mixing parts, which is applied in the field of raw material extrusion machines, can solve the problems of inability to remodel, increase the cost of mixers, and complicate CTM installation, and achieve the effect of less cost and shorter overall length
- Summary
- Abstract
- Description
- Claims
- Application Information
AI Technical Summary
Problems solved by technology
Method used
Image
Examples
Embodiment Construction
[0051] Objects and advantages of the present invention will become apparent from the following detailed description taken in conjunction with the accompanying drawings, in which FIG. 1 shows a mixer 10 of the present invention, used in the manner of a screw extruder 8 . In the screw extruder 8 , a central screw 14 comprises a central shaft 16 with a plurality of protruding mixing elements 18 arranged in a mixing section 20 . It should be understood that the screw 14 may preferably have additional portions thereon that are primarily concerned with conveying the material, one such conveying portion 22 shown having conveying threads 24 . The mixing section 20 of the central screw 14 is partially surrounded by a jacket 12 having a jacket body 26 and protruding mixing elements 28 which preferably face inwardly, towards the central screw 14 . The protruding mixing elements 18, 28 on the screw 14 and the sleeve are staggered relative to each other in a radial manner so that the relat...
PUM
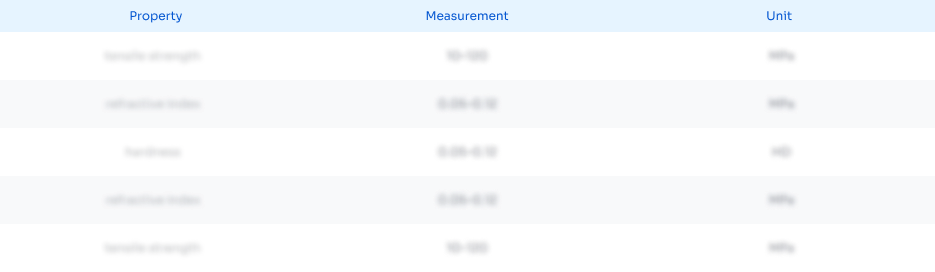
Abstract
Description
Claims
Application Information

- R&D
- Intellectual Property
- Life Sciences
- Materials
- Tech Scout
- Unparalleled Data Quality
- Higher Quality Content
- 60% Fewer Hallucinations
Browse by: Latest US Patents, China's latest patents, Technical Efficacy Thesaurus, Application Domain, Technology Topic, Popular Technical Reports.
© 2025 PatSnap. All rights reserved.Legal|Privacy policy|Modern Slavery Act Transparency Statement|Sitemap|About US| Contact US: help@patsnap.com