Preparation method for hollow fiber osmosis vaporation permeable complex film
A pervaporation and composite membrane technology, which is applied in the field of separation membrane preparation, can solve the problems of difficult industrial application, large footprint of membrane modules, and low mechanical strength, and achieve good uniformity, repeatability, convenient operation, and low price. Effect
- Summary
- Abstract
- Description
- Claims
- Application Information
AI Technical Summary
Problems solved by technology
Method used
Examples
Embodiment 1
[0024] Weigh 20g of polyvinyl alcohol (PVA-1799), add 980g of distilled water, stir at a constant temperature of 85°C, and continue stirring for 20 to 30 minutes after the PVA is completely dissolved. Keep the container sealed during stirring to avoid evaporation of water at high temperatures. The resulting solution was suction filtered to remove insoluble matter, and the filtrate was set aside. Weigh 5g of sodium alginate, add 245g of distilled water, stir and dissolve at room temperature, and filter the obtained solution to remove insoluble matter. Blend the above two filtrates, add 18.75g of maleic anhydride, stir at a constant temperature of 30°C, and let the obtained solution stand or pump After vacuum defoaming, the film-making solution was made. Soak the polyacrylonitrile ultrafiltration membrane in 3wt% NaOH aqueous solution, keep it at room temperature for 1 hour, wash it with distilled water to neutral after taking it out, and dry it at room temperature for use. Im...
Embodiment 2
[0028] Weigh 20g of polyvinyl alcohol (PVA-1799), add 980g of distilled water, stir at a constant temperature of 85°C, and continue stirring for 20 to 30 minutes after the PVA is completely dissolved. Keep the container sealed during stirring to avoid evaporation of water at high temperatures. The resulting solution was suction filtered to remove insoluble matter, and the filtrate was set aside. Weigh 5g of sodium alginate, add 245g of distilled water, stir and dissolve at room temperature, and filter the resulting solution to remove insoluble matter. The above two filtrates are blended, and the resulting solution is left to stand or vacuumed for defoaming. Soak the polyacrylonitrile ultrafiltration membrane (base membrane) in 3wt% NaOH aqueous solution, keep it at room temperature for 1 hour, wash it with distilled water to neutral after taking it out, and dry it in room temperature. Immerse the treated basement membrane in the membrane-forming solution for 3-5 seconds, tak...
Embodiment 3
[0032]Weigh 50g of polyvinyl alcohol (PVA-1799), add 950g of distilled water, stir at a constant temperature of 85°C, and continue stirring for 20 to 30 minutes after the PVA is completely dissolved. Keep the container sealed during stirring to avoid evaporation of water at high temperatures. The resulting solution was suction filtered to remove insoluble matter, and the filtrate was set aside. Weigh 12.5g of sodium alginate, add 237.5g of distilled water, stir and dissolve at room temperature, and filter the resulting solution to remove insoluble matter. The above two filtrates were blended, 37.5 g of maleic anhydride was added, and stirred at a constant temperature of 30° C., and the obtained solution was left to stand or vacuumed for degassing, and then the film could be scraped. Soak the polyacrylonitrile ultrafiltration membrane in 3wt% NaOH aqueous solution, keep it at room temperature for 1 hour, wash it with distilled water to neutral after taking it out, and dry it a...
PUM
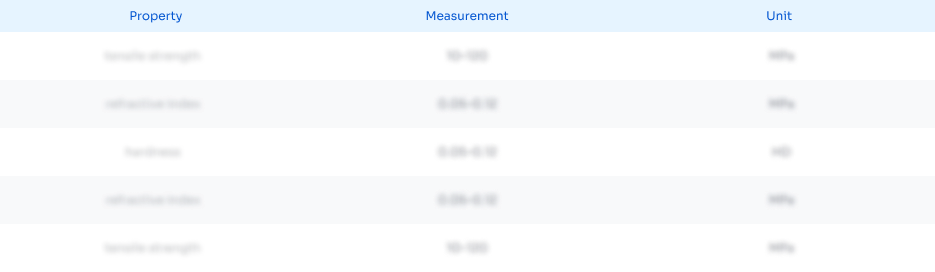
Abstract
Description
Claims
Application Information

- R&D Engineer
- R&D Manager
- IP Professional
- Industry Leading Data Capabilities
- Powerful AI technology
- Patent DNA Extraction
Browse by: Latest US Patents, China's latest patents, Technical Efficacy Thesaurus, Application Domain, Technology Topic, Popular Technical Reports.
© 2024 PatSnap. All rights reserved.Legal|Privacy policy|Modern Slavery Act Transparency Statement|Sitemap|About US| Contact US: help@patsnap.com