Methods and apparatus for providing touch-sensitive input in multiple degrees of freedom
a technology of input control and multiple degrees of freedom, applied in the field of input control devices with multiple surfaces, can solve the problems of user fatigue, cumbersome 3d and 6d input devices, and inability to refine, improve accuracy, and ease of use of existing 2d input devices,
- Summary
- Abstract
- Description
- Claims
- Application Information
AI Technical Summary
Benefits of technology
Problems solved by technology
Method used
Image
Examples
first embodiment
[0116]FIG. 1 is an illustration of a force / touch sensitive 3D controller in accordance with the present invention. A controller 105 is shaped substantially in the form of a cube having six faces or sides, i.e. controller 105 can be provided as a cube shape or other similar shapes, such as a rectilinear object or cube having rounded edges or the like. Alternatively, controller 105 can have other shapes. A first force-sensitive sensor pad 110 is positioned on the front face of controller 105. A second force-sensitive sensor pad 115 is positioned on the right side of controller 105. A third force-sensitive sensor pad 120 is positioned on the top side of controller 105. A fourth force-sensitive sensor pad 125 is positioned on the left side of controller 105. A fifth force-sensitive sensor pad 130 is positioned on the back side of controller 105. A sixth force-sensitive sensor pad 135 is positioned on the bottom side of controller 105. A frame 140 is attached to the edge of controller 10...
second embodiment
[0122]FIG. 3 is an illustration of a force / touch sensitive 6D controller in accordance with the present invention. Controller 305 is also shaped in the form of a cube, however this controller uses three force-sensitive matrix sensors. A first force-sensitive matrix sensor 310 is positioned on the front of controller 205. Sensor 310 provides two analog signals in response to the position of an applied force, which provides X and Y position information as illustrated in FIG. 4a. Sensor 310 also provides a third signal is response to the magnitude of the force applied to sensor 310. A second force-sensitive matrix sensor 315 is positioned on the right side of controller 305. Sensor 315 provides two analog signals in response to the position of the force applied to sensor 315, which will be interpreted by control electronics to provide Y and Z information as illustrated in FIG. 4a. Sensor 315 also provides a third signal responsive to the magnitude of the force applied to sensor 315. A ...
third embodiment
[0127]FIG. 6 illustrates a 6D controller 605. Controller 605 is shaped substantially in the form of a cube. A first force-sensitive matrix sensor 610 is positioned on the front of controller 605. A second force-sensitive matrix sensor 615 is positioned on the right side of controller 605. A third force-sensitive matrix sensor 620 is positioned on the top side of controller 605. A fourth force-sensitive matrix sensor 625 is positioned on the left side of controller 605. A fifth force-sensitive matrix sensor 630 is positioned on the back side of controller 605. A sixth force-sensitive matrix sensor 635 is positioned on the bottom side of controller 605. A frame 640 is attached to the edge of controller 605 between the bottom and back surfaces, allowing the user to access to all six surfaces of controller 605. Control harness 645 is coupled to force-sensitive matrix sensor 610, 615, 620, 625, 630, and 635 and provides signals indicative of the magnitude and the position of the force ap...
PUM
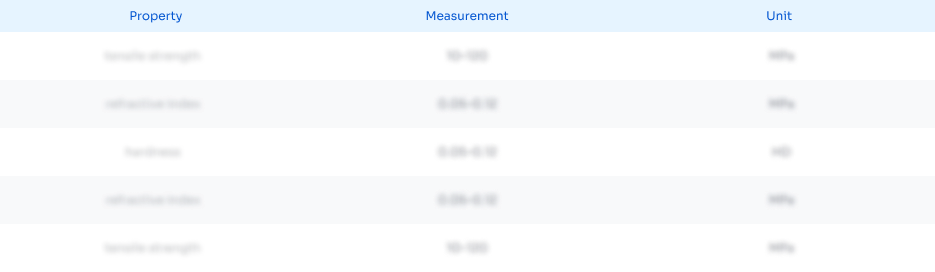
Abstract
Description
Claims
Application Information

- R&D
- Intellectual Property
- Life Sciences
- Materials
- Tech Scout
- Unparalleled Data Quality
- Higher Quality Content
- 60% Fewer Hallucinations
Browse by: Latest US Patents, China's latest patents, Technical Efficacy Thesaurus, Application Domain, Technology Topic, Popular Technical Reports.
© 2025 PatSnap. All rights reserved.Legal|Privacy policy|Modern Slavery Act Transparency Statement|Sitemap|About US| Contact US: help@patsnap.com