Apparatus for cutting rumble strips in a road surface
a technology for rumble strips and apparatuses, applied in cutting machines, roads, construction, etc., can solve the problems of reducing the effectiveness of rumble strips, rolling drums used on asphaltic roads, etc., and achieve the effect of easy removal of debris, convenient observation, and reduced areas
- Summary
- Abstract
- Description
- Claims
- Application Information
AI Technical Summary
Benefits of technology
Problems solved by technology
Method used
Image
Examples
Embodiment Construction
[0022]Referring now to the drawings in greater detail, and initially to FIG. 1, a cutting head used to mill rumble strip depressions in accordance with the present invention is represented broadly by the numeral 10. The cutting head 10 is designed to be rotated about a center rotational axis 12 as it is moved up and down to mill away portions of a road surface to form the rumble strip depressions in the road.
[0023]The cutting head 10 has a preselected length along its rotational axis 12 and a transverse diameter that varies along the length of the rotational axis 12. As used herein, the transverse diameter is understood to be taken in a plane perpendicular to the rotational axis 12. In the preferred embodiment, the smallest transverse diameter is at opposite ends 14 and 15 of the cutting head 10 and the greatest transverse diameter is midway between the ends 14 and 15. It will be appreciated that the areas of smallest and greatest transverse diameter can be shifted along the axis 12...
PUM
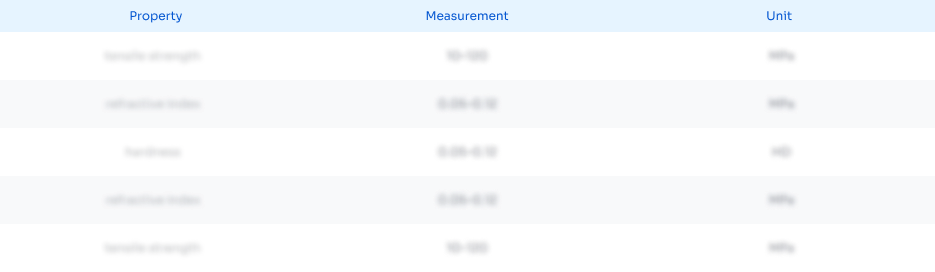
Abstract
Description
Claims
Application Information

- R&D
- Intellectual Property
- Life Sciences
- Materials
- Tech Scout
- Unparalleled Data Quality
- Higher Quality Content
- 60% Fewer Hallucinations
Browse by: Latest US Patents, China's latest patents, Technical Efficacy Thesaurus, Application Domain, Technology Topic, Popular Technical Reports.
© 2025 PatSnap. All rights reserved.Legal|Privacy policy|Modern Slavery Act Transparency Statement|Sitemap|About US| Contact US: help@patsnap.com