Drive apparatus
a drive apparatus and drive shaft technology, applied in piezoelectric/electrostrictive/magnetostrictive devices, piezoelectric/electrostrictive/magnetostriction machines, piezoelectric/electrostrictive/magnetostrictive devices, etc., can solve the problem of large rush-current flows, power consumption becomes high, and the suppressing effect of rush-current is not sufficient, so as to achieve accurate driving. the effect of easy and efficient execution
- Summary
- Abstract
- Description
- Claims
- Application Information
AI Technical Summary
Benefits of technology
Problems solved by technology
Method used
Image
Examples
second embodiment
Next, there will be explained below the drive apparatus according to the present invention with reference to FIGS. 5 and 6.
The drive apparatus according to the second embodiment is constituted approximately similarly to the drive apparatus of the first embodiment, but there is a difference such that the switching elements Q5 and Q6 in FIG. 3 are omitted and the switching elements Q2 and Q4 serve also as them. The following will mainly explain the different point using the like reference numerals for the like components.
FIG. 5 shows a drive circuit 30a of the drive apparatus according to the second embodiment. The drive circuit 30a omits a switching element for a discharging circuit and includes four switching elements Q1, Q2, Q3 and Q4, inductive elements G1 and G2 and a control circuit 32a. The switching elements Q1 through Q4 compose the first and second drive circuits approximately similarly to the first embodiment. Differently from the first embodiment, the inductive element G1 ...
PUM
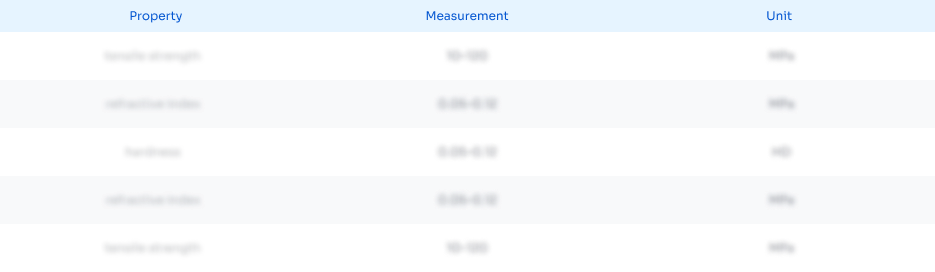
Abstract
Description
Claims
Application Information

- R&D
- Intellectual Property
- Life Sciences
- Materials
- Tech Scout
- Unparalleled Data Quality
- Higher Quality Content
- 60% Fewer Hallucinations
Browse by: Latest US Patents, China's latest patents, Technical Efficacy Thesaurus, Application Domain, Technology Topic, Popular Technical Reports.
© 2025 PatSnap. All rights reserved.Legal|Privacy policy|Modern Slavery Act Transparency Statement|Sitemap|About US| Contact US: help@patsnap.com