Lubrication-free centrifugal compressor
a centrifugal compressor and lubrication-free technology, which is applied in the direction of non-positive displacement fluid engines, radial flow pumps, pump components, etc., can solve the problems of high maintenance requirements of the lubrication system, the most bulky of the four types of alternative compressors, and the most mechanical wear of the above mentioned components, etc., to achieve high efficiency, high electric frequency, and high speed
- Summary
- Abstract
- Description
- Claims
- Application Information
AI Technical Summary
Benefits of technology
Problems solved by technology
Method used
Image
Examples
Embodiment Construction
[0029]The present invention is a compact device for gas compression driven by an axial flow synchronous electric motor with no use of any kind of lubricants.
[0030]FIG. 1 shows the single mobile piece of the motor-impeller rotating assembly (hereinafter, the rotor). Said rotor has a centrifugal impeller 1 in charge of delivering kinetic energy to the process gas. In the embodiment of FIG. 1 only one impeller is shown but more than one may be used. Said impeller is mounted on an axis 5 and fixed thereto. If more than one impeller is used, all of them may be mounted on and fixed to the same axis.
[0031]An axial flow synchronous and permanent magnet electric motor 2 is formed by a stationary stator section and a rotating section. The stator section of said motor contains the coils, different auxiliary pieces for support and may optionally contain part of the ferromagnetic core. This section may be formed by one or more assemblies located between assemblies of a rotating section. In the e...
PUM
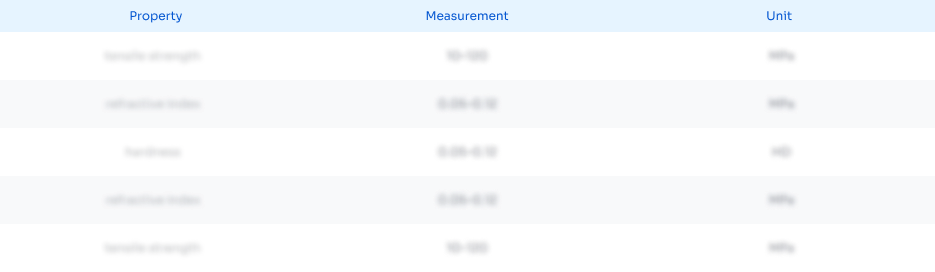
Abstract
Description
Claims
Application Information

- R&D
- Intellectual Property
- Life Sciences
- Materials
- Tech Scout
- Unparalleled Data Quality
- Higher Quality Content
- 60% Fewer Hallucinations
Browse by: Latest US Patents, China's latest patents, Technical Efficacy Thesaurus, Application Domain, Technology Topic, Popular Technical Reports.
© 2025 PatSnap. All rights reserved.Legal|Privacy policy|Modern Slavery Act Transparency Statement|Sitemap|About US| Contact US: help@patsnap.com