In-line strainer with tension control mechanisms for use on high tensile wire
- Summary
- Abstract
- Description
- Claims
- Application Information
AI Technical Summary
Benefits of technology
Problems solved by technology
Method used
Image
Examples
first embodiment
[0090]As shown by a first embodiment in FIGS. 2 and 3, and in more detail on a component by component basis in FIGS. 4-10C, the present invention is directed to an in-line strainer, generally designated by reference numeral 10, for placement within a span of wire fence to apply tension thereto. The in-line strainer 10 includes a body or strap generally designated by reference numeral 12, a reel 14, a torque limiting mechanism generally designated by reference numeral 16, and a reel holding mechanism generally designated by reference numeral 18.
[0091]The strap 12 can be a unified member or, as shown in FIGS. 3, 4 and 4A-4F, may be comprised of two separate strap members 12a and 12b that are connected to one another when the strainer is assembled as shown in FIG. 2. The two strap members are identical which facilitates ease of manufacture, with each strap member having a body 20 with an axle mounting aperture 22, a pawl mounting aperture 24, a pair of pawl spring mounting loops 26, an...
fifth embodiment
[0114]the torque limiting mechanism in accordance with the present invention is illustrated in FIGS. 23-25 and generally designated by reference numeral 500. A compression spring 552 is sandwiched between two pressure plates 553 and secured within the hollow central portion 540 of the reel by nuts 550. The pressure plates 553 are provided with peripheral detents 554 that engage corresponding notches 544 in the reel inner wall 542. A shoulder screw 557 is inserted through aligned apertures 559 in the pressure plates 553 and twisted to compress the spring 552. Upon sufficient compression of the spring, the detents 554 on the pressure plates will disengage from the reel notches 544 in a manner similar to the previous embodiments.
sixth embodiment
[0115]the torque limiting mechanism according to the present invention is illustrated in FIGS. 26-28 and generally designated by reference numeral 600. In this embodiment, the axle is formed by two nuts 650 which serve as the tool engagement heads on either side of the reel 614. A urethane spring 652 is inserted into the bore 651 of each of the nuts 650 and then tightened to the desired degree with a respective shoulder screw 657. The nuts 650 are rotated to turn the reel 614 and tension the wire until the springs 652 exceed the frictional forces preventing rotation and allow “slip” within the bores.
[0116]A seventh embodiment of the torque limiting mechanism in accordance with the present invention is illustrated in FIGS. 29-31 and generally designated by reference numeral 700. This embodiment operates similarly to the sixth embodiment, except that the axle does not go all the way through the reel 714. Belleville springs 752 are compressed by shoulder screw 757 until interference su...
PUM
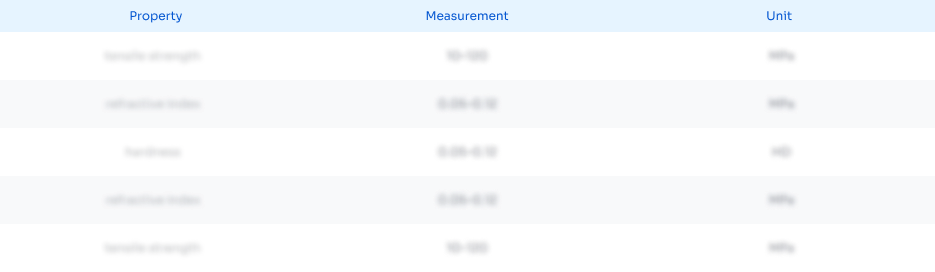
Abstract
Description
Claims
Application Information

- R&D
- Intellectual Property
- Life Sciences
- Materials
- Tech Scout
- Unparalleled Data Quality
- Higher Quality Content
- 60% Fewer Hallucinations
Browse by: Latest US Patents, China's latest patents, Technical Efficacy Thesaurus, Application Domain, Technology Topic, Popular Technical Reports.
© 2025 PatSnap. All rights reserved.Legal|Privacy policy|Modern Slavery Act Transparency Statement|Sitemap|About US| Contact US: help@patsnap.com