Multiple clutch device
a multi-claw technology, applied in the direction of yielding couplings, couplings, mechanical devices, etc., can solve the problems of increasing the axial construction space requirement of dual clutches, increasing the unsteady running of the drive units, and increasing the unsteady running of the drive units. , to achieve the effect of increasing the unsteady running of the drive units, and reducing the overall number of cylinders
- Summary
- Abstract
- Description
- Claims
- Application Information
AI Technical Summary
Benefits of technology
Problems solved by technology
Method used
Image
Examples
Embodiment Construction
[0027]FIG. 1 shows a dual clutch 1 composed of two radially nested wet-running multi-plate clutches K1 and K2. Clutch K1 is in this case arranged radially on the outside and clutch K2 radially on the inside. The dual clutch 1 is driven by an output hub 2 of a two-mass flywheel (not shown in detail) preceding the clutch 1.
[0028]Between this two-mass flywheel and the dual clutch 1 is located a clutch cover 3 which separates a wet space 4 from a dry space 5. Static sealing 6 of the clutch cover 3 with respect to a transmission housing 7 of a transmission (not shown in detail) following in the drive train takes place preferably via an O-ring 6 or another static sealing element.
[0029]Sealing with respect to the dual clutch 1 takes place preferably via a radial shaft sealing ring 8 as a dynamic sealing element.
[0030]The output hub 2 of the two-mass flywheel (also designated below briefly as ZMS) is connected fixedly in terms of rotation to a clutch hub 9 via a toothing. The clutch hub 9 i...
PUM
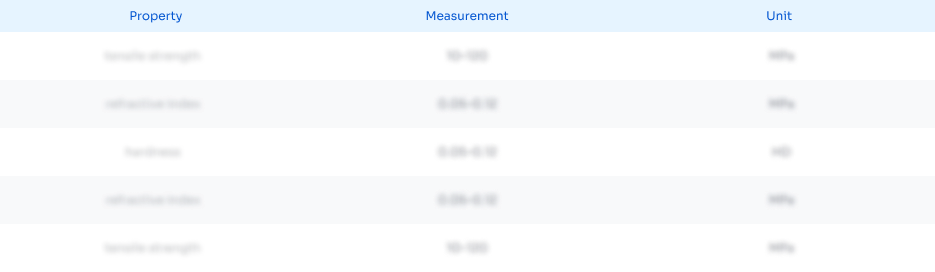
Abstract
Description
Claims
Application Information

- R&D
- Intellectual Property
- Life Sciences
- Materials
- Tech Scout
- Unparalleled Data Quality
- Higher Quality Content
- 60% Fewer Hallucinations
Browse by: Latest US Patents, China's latest patents, Technical Efficacy Thesaurus, Application Domain, Technology Topic, Popular Technical Reports.
© 2025 PatSnap. All rights reserved.Legal|Privacy policy|Modern Slavery Act Transparency Statement|Sitemap|About US| Contact US: help@patsnap.com