Embedded arm strain sensors
a technology of strain gage and embedded arm, which is applied in the direction of program control, instruments, testing/monitoring control systems, etc., can solve the problems of relatively difficult use of measurement installations and high cos
- Summary
- Abstract
- Description
- Claims
- Application Information
AI Technical Summary
Benefits of technology
Problems solved by technology
Method used
Image
Examples
Embodiment Construction
[0015]Exemplary embodiments include systems and methods for measuring strain on arm segments of a portable articulated arm coordinate measuring machine either to compensate measurement results to improve accuracy or to alert the operator of the need for corrective action.
[0016]FIGS. 1A and 1B illustrate, in perspective, a portable articulated arm coordinate measuring machine (AACMM) 100 according to various embodiments of the present invention, an articulated arm being one type of coordinate measuring machine. As shown in FIGS. 1A and 1B, the exemplary AACMM 100 may comprise a six or seven axis articulated measurement device having a measurement probe housing 102 coupled to an arm portion 104 of the AACMM 100 at one end. The arm portion 104 comprises a first arm segment 106 coupled to a second arm segment 108 by a first grouping of bearing cartridges 110 (e.g., two bearing cartridges). A second grouping of bearing cartridges 112 (e.g., two bearing cartridges) couples the second arm ...
PUM
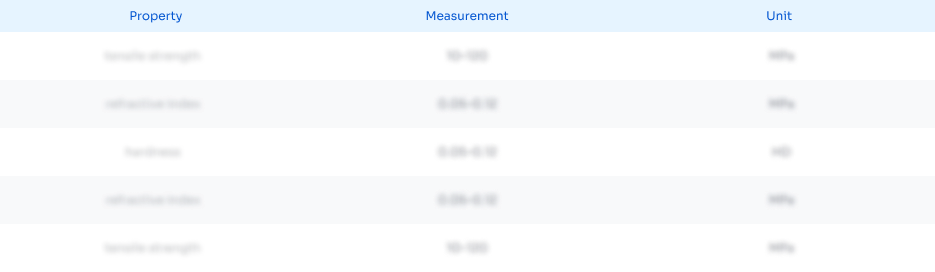
Abstract
Description
Claims
Application Information

- R&D
- Intellectual Property
- Life Sciences
- Materials
- Tech Scout
- Unparalleled Data Quality
- Higher Quality Content
- 60% Fewer Hallucinations
Browse by: Latest US Patents, China's latest patents, Technical Efficacy Thesaurus, Application Domain, Technology Topic, Popular Technical Reports.
© 2025 PatSnap. All rights reserved.Legal|Privacy policy|Modern Slavery Act Transparency Statement|Sitemap|About US| Contact US: help@patsnap.com