Method and apparatus for gas flow control
a flow control and flow rate technology, applied in the direction of engine diaphragms, diaphragm valves, instruments, etc., can solve the problems of difficult change or control of the physical properties of the gas and the temperature of the system, unable to monitor or control the characteristics of critical orifice devices, and the actual flow rate through the mfc can drift to unacceptable values, etc., to achieve a high degree of precision
- Summary
- Abstract
- Description
- Claims
- Application Information
AI Technical Summary
Benefits of technology
Problems solved by technology
Method used
Image
Examples
Embodiment Construction
[0037]Embodiments of the present invention provide for a controllable flow restriction in which the dimensions of the flow restriction are measurable and controllable to a very high degree of precision. The measurement and control of the dimensions are precise enough that they can be used to accomplish the self-calibrating gas-flow-control scheme shown in FIG. 1 with the flow accuracy required by the semiconductor industry.
[0038]In various embodiments of the present invention, this level of precision is obtained by incorporating the following characteristics:[0039]1. Uniaxial motion of the two opposing faces of the flow restriction, where transverse and / or rotational motion in the other two axes is limited to less than approximately 1 nm;[0040]2. Measurement of motion in the uniaxial dimension to a precision of approximately 1 nm;[0041]3. Actuation of motion with resolution of approximately 0.1 nm.
[0042]An illustrative embodiment of the invention, shown in FIG. 2, consists of two ad...
PUM
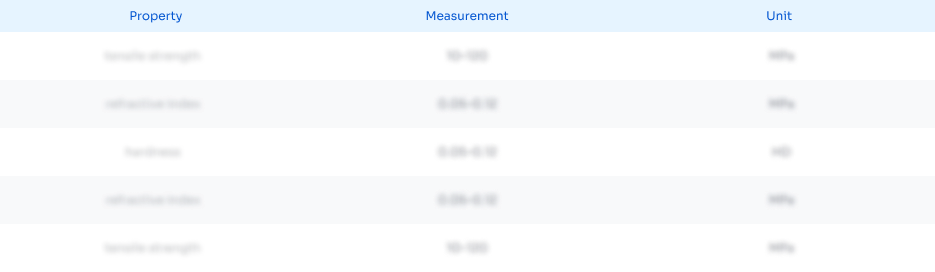
Abstract
Description
Claims
Application Information

- R&D
- Intellectual Property
- Life Sciences
- Materials
- Tech Scout
- Unparalleled Data Quality
- Higher Quality Content
- 60% Fewer Hallucinations
Browse by: Latest US Patents, China's latest patents, Technical Efficacy Thesaurus, Application Domain, Technology Topic, Popular Technical Reports.
© 2025 PatSnap. All rights reserved.Legal|Privacy policy|Modern Slavery Act Transparency Statement|Sitemap|About US| Contact US: help@patsnap.com