Viv and/or drag reduction device installation systems and methods
a technology of drag reduction device and installation system, which is applied in waterborne vessels, construction, foundation engineering, etc., can solve the problems of large vibration transverse to current, unacceptably short fatigue life, and substantial vibration of structural elements, and achieve the effect of fewer trips
- Summary
- Abstract
- Description
- Claims
- Application Information
AI Technical Summary
Benefits of technology
Problems solved by technology
Method used
Image
Examples
Embodiment Construction
[0028]Referring now to FIG. 2, in one embodiment of the invention, system 200 is illustrated. System 200 includes vessel 210 in body of water 212, installing VIV and / or drag reduction devices 224a-224e, for example strakes or fairings, on structural element 214. As shown, structural element 214 may be a riser, tendon, connector, tubular, umbilical, or other structural or fluid transportation member, and may be connected to surface structure 215. Remotely operated vehicle (ROV) 220 is connected by umbilical 221 to vessel 210. ROV 220 is also connected to installation tool 222, to install VIV and / or drag reduction device 224c on structural element 214. Transport tool 226 is connected by line 227 to vessel 210. In some embodiments, line 227 may be an umbilical, a rope, a cable, a wire, or others as are known in the art. Transport tool is used to transport VIV and / or drag reduction devices 224d and 224e from vessel 210 to near desired location of structural element 214.
[0029]In some emb...
PUM
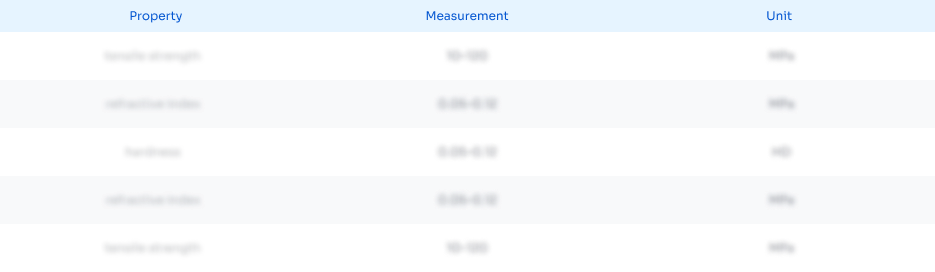
Abstract
Description
Claims
Application Information

- R&D
- Intellectual Property
- Life Sciences
- Materials
- Tech Scout
- Unparalleled Data Quality
- Higher Quality Content
- 60% Fewer Hallucinations
Browse by: Latest US Patents, China's latest patents, Technical Efficacy Thesaurus, Application Domain, Technology Topic, Popular Technical Reports.
© 2025 PatSnap. All rights reserved.Legal|Privacy policy|Modern Slavery Act Transparency Statement|Sitemap|About US| Contact US: help@patsnap.com