Modular building construction employing concrete mold assembly
a technology of concrete molds and modular components, applied in special buildings, parkings, walls, etc., can solve the problem of more difficult construction of modular components under the same limitations
- Summary
- Abstract
- Description
- Claims
- Application Information
AI Technical Summary
Benefits of technology
Problems solved by technology
Method used
Image
Examples
Embodiment Construction
[0102] The self-contained mold according to the invention is formed by installation of two or more wall panels or the wall of several modular components placed adjacent to one another, however spaced apart to allow for concrete to form between the panels or modules. The wall sections can be composed of metal construction or wood construction with the interior finish, preferably, to be the interior finish of the structure. The structural wood studs or steel studs, as well as the interior finish material, as a part of the structure and are not removed. Both galvanized steel, or wood fire rating capabilities, however, are nothing like the fire rating of concrete. The encasement of the steel studs or wood studs into concrete, increasing the structural capacity, as well as increasing the fire rating of the wall component. The prevention of air around the wall studs decreases the cause for a fire to start. Increasing the size of wood studs increases the strength and decreases the gauge si...
PUM
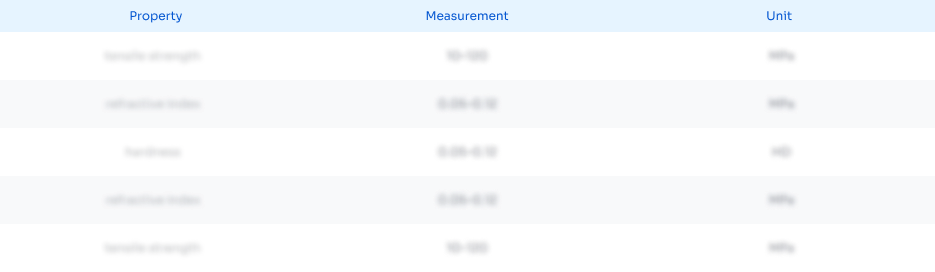
Abstract
Description
Claims
Application Information

- R&D
- Intellectual Property
- Life Sciences
- Materials
- Tech Scout
- Unparalleled Data Quality
- Higher Quality Content
- 60% Fewer Hallucinations
Browse by: Latest US Patents, China's latest patents, Technical Efficacy Thesaurus, Application Domain, Technology Topic, Popular Technical Reports.
© 2025 PatSnap. All rights reserved.Legal|Privacy policy|Modern Slavery Act Transparency Statement|Sitemap|About US| Contact US: help@patsnap.com