Motion control systems and methods
a technology of motion control and control system, applied in the direction of program control, electric programme control, instruments, etc., can solve the problems of not providing the application programmer with the ability to control the hardware in base incremental steps, and the software driver model currently used for printers and the like is not applicable to the development of a sequence of control commands for motion control devices
- Summary
- Abstract
- Description
- Claims
- Application Information
AI Technical Summary
Benefits of technology
Problems solved by technology
Method used
Image
Examples
example 1
[0326] The first example illustrates how the language driver 44 might deal with the Driver function IXMC_DrvExt_Test::Move.
Cmd Format: D % d,+:@[snd]GO%b+:@[snd]
Rsp Format: @[crlf]>@[rcv]@[crlf]>@[rcv]
Driver function Call: pXMCDrvExtTest->Move(20.0, 30.0)
[0327] This function call directs the motion control device to move 20 units in the x direction and 30 units in the y direction.
[0328] The driver communicates with the stream as follows:
[0329] Step 1. Perform the operation in the command format template up to the first @ symbol. This builds a raw command string of “D20.0,30.0:”
[0330] Step 2. After the first @ symbol is the send command, which sends the string that was built in step 1. The language driver has now reached the G in the command format template.
[0331] Step 3. After the send command, the language driver reads a response from the stream to confirm that the command string was received and processed correctly. The response string received from the stream is as follow...
example 2
[0336] The second example illustrates how the language driver 44 might deal with the Driver function IXMC_DrvExt_Test::SetVelocity.
Cmd Format: V%If,+:@[snd]
Rsp Format: @[crlf]>@[rcv]
Driver function Call: pXMCDrvExtTest->SetVelocity(NOP, 22.0)
Explanation Set the velocity of the y axis to 22.0.
Raw Command String: “V,22.0:”
Raw Response String: “\r\n>” (expected)
example 3
[0337] The third example illustrates how the language driver 44 might deal with the Driver function
IXMC_DrvExt_Test::GetVelocity.
Cmd Format: GV%b+:@[snd]
Rsp Format: % d,+@[crlf]>@[rcv]
Driver function Call: pXMCDrvExtTest->GetVelocity(NOP, &dfY_Vel)
Explanation Get the velocity set for the y axis.
Raw Command String: “GV01:”
Raw Response String: “,44.0\r\n>” (expected)
dfY_Vel=44.0
PUM
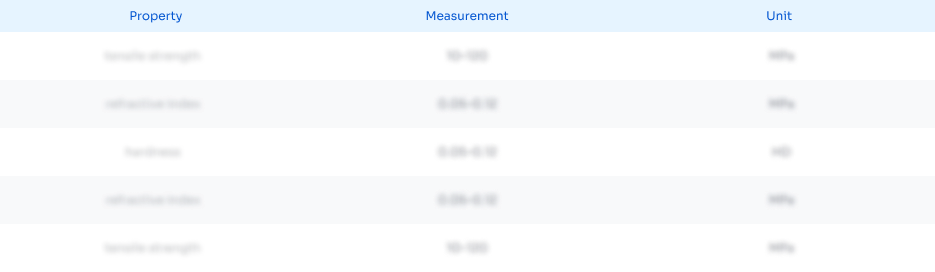
Abstract
Description
Claims
Application Information

- R&D
- Intellectual Property
- Life Sciences
- Materials
- Tech Scout
- Unparalleled Data Quality
- Higher Quality Content
- 60% Fewer Hallucinations
Browse by: Latest US Patents, China's latest patents, Technical Efficacy Thesaurus, Application Domain, Technology Topic, Popular Technical Reports.
© 2025 PatSnap. All rights reserved.Legal|Privacy policy|Modern Slavery Act Transparency Statement|Sitemap|About US| Contact US: help@patsnap.com