Improved shotgun barrel construction
a barrel and shotgun technology, applied in the field of improved shotgun barrel construction, can solve the problems of affecting the quality of finished products, and requiring considerable handwork, so as to reduce the recoil of felt, reduce the cost of production, and reduce the effect of manufacturing cos
- Summary
- Abstract
- Description
- Claims
- Application Information
AI Technical Summary
Benefits of technology
Problems solved by technology
Method used
Image
Examples
Embodiment Construction
[0051] A complete barrel assembly is illustrated in the FIG. 1 perspective view of a multi-barreled shotgun barrel assembly.
[0052] The barrel assembly is simplified into four main components in the FIG. 2 exploded view of the barrel assembly. These components are the Extended Chopper Block 1, the Upper Barrel Tube 2A, the Lower Barrel Tube 2B, the Muzzle Block 3, and the Top Rib Sighting Plane 4.
[0053]FIG. 3, exploded cross-sectional view of the barrel assembly, illustrates the internal features and characteristics of this type of barrel construction. The Extended Chopper Block 1 has a length sufficient to for a Shot Shell Chamber Area 12 providing for shot shells of all lengths along with an Extended or Long Forcing Cone Area 13 which transitions the shot column when the shotgun is fired from the chamber internal diameter to the Barrel Bore in the Extended Chopper Block 14A. This Extended Chopper Block construction contains all forces produced when firing the shot shells in the g...
PUM
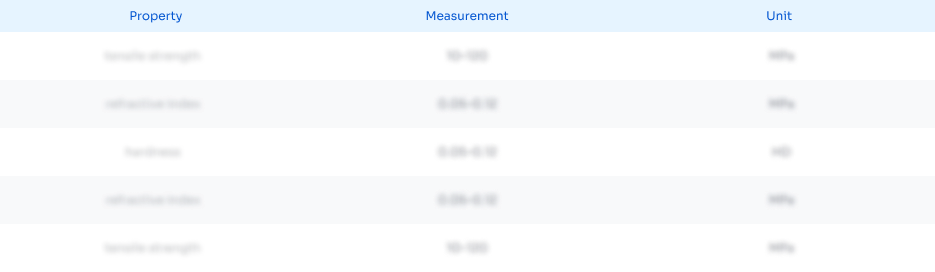
Abstract
Description
Claims
Application Information

- R&D
- Intellectual Property
- Life Sciences
- Materials
- Tech Scout
- Unparalleled Data Quality
- Higher Quality Content
- 60% Fewer Hallucinations
Browse by: Latest US Patents, China's latest patents, Technical Efficacy Thesaurus, Application Domain, Technology Topic, Popular Technical Reports.
© 2025 PatSnap. All rights reserved.Legal|Privacy policy|Modern Slavery Act Transparency Statement|Sitemap|About US| Contact US: help@patsnap.com