Apparatus for tightening threaded member
a technology for threaded members and actuators, which is applied in the direction of power driven tools, metal-working apparatus, wrenches, etc., can solve the problems of manual operation of temporary tightening operation with tiresome and troublesome, requiring certain time and burden, and affecting the engine's productivity, etc., and achieves smooth loosening
- Summary
- Abstract
- Description
- Claims
- Application Information
AI Technical Summary
Benefits of technology
Problems solved by technology
Method used
Image
Examples
first embodiment
[0056] Referring to FIG. 1, there is shown an apparatus 10 for tightening a threaded member according to the present invention. In the illustrated embodiment, the threaded member is a hexagon head bolt 13. The apparatus 10 includes a screwing mechanism 18 having a rotational shaft 19, and an automatic robot arm 16 (axially moving means for moving axially to rotate the rotational shaft 19). The screwing mechanism 18 is mounted via a bracket 17 to a lower end 16a of the arm 16. The apparatus 10 further includes a shaft member 20 pivotably connected to a lower end of the rotational shaft 19 of the screwing mechanism 18. The robot arm 16 is arranged to move axially of the rotational shaft 19 so as to rotate the shaft 19. That is, the axial movement of the arm 16 is converted to rotation of the rotational shaft 19. The shaft member 20 has a socket portion 21 provided at a distal end thereof. The socket portion 21 is designed or sized to receive a head 14 of the bolt 13 therein. As will b...
second embodiment
[0153] In the second embodiment, the inner periphery 147a is formed to provide the hexagonal cross-section, but may be of circular, octagonal or other polygonal cross-section to serve the same function as discussed above.
[0154] Referring to FIG. 17, the lower cylinder member 137 includes a cylinder body 148. The cylinder body 148 has its inner periphery 148a formed to provide a hexagonal cross-section.
[0155] The slider 140 is a pipe of hexagonal cross-section and is telescoped or inserted into the cylinder body 148.
[0156] The cylinder body 148 has mounting apertures 148b, 148b formed to laterally extend therethrough. The slider 140 has mounting apertures 140d, 140d formed to laterally extend therethrough. The mounting bolt 141 is inserted through the apertures 148b, 148b, 140d, 140d.
[0157] The mounting bolt 141 has a nut 152 tightened thereonto to mount the slider 140 to the cylinder body 148.
[0158] Providing the inner periphery 148a and the slider 140 with the hexagonal configu...
PUM
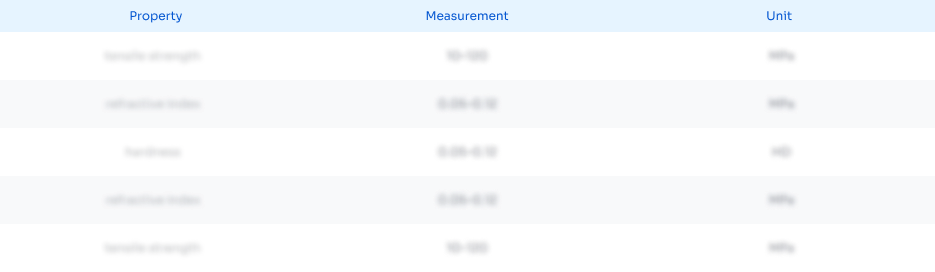
Abstract
Description
Claims
Application Information

- R&D
- Intellectual Property
- Life Sciences
- Materials
- Tech Scout
- Unparalleled Data Quality
- Higher Quality Content
- 60% Fewer Hallucinations
Browse by: Latest US Patents, China's latest patents, Technical Efficacy Thesaurus, Application Domain, Technology Topic, Popular Technical Reports.
© 2025 PatSnap. All rights reserved.Legal|Privacy policy|Modern Slavery Act Transparency Statement|Sitemap|About US| Contact US: help@patsnap.com