Truss manufacturing method and system
a manufacturing method and a technology for trusses, applied in the direction of girders, joists, buildings, etc., can solve the problems of less efficient in terms of stud material, less efficient in terms of span and load capacity of frame trusses, and more difficult design and assembly of back-to-back trusses
- Summary
- Abstract
- Description
- Claims
- Application Information
AI Technical Summary
Benefits of technology
Problems solved by technology
Method used
Image
Examples
Embodiment Construction
[0016] With reference to FIGS. 1A-1C, an exemplary roofing truss 100 made in accordance with an embodiment of the present invention is shown. Truss 100 is a conventional roof truss made from roll-formed, structural stud members connected in a back-to-back configuration. It generally comprises a lower C-channel chord member 102, upper C-channel chord members 104, 106, and C-channel web members 101 to 117. The centerlines for each member are shown, along with connection nodes N1 to N18.
[0017] Truss 100 is a conventional roof truss formed, e.g., from light gauge (22 to 12 .ga) steel stud members, but it is formed using techniques of the present invention and takes advantage of features available on conventional roll-forming machines. Namely, the machine is used not only to form and cut each truss member into its proper dimensions, but also, it applies an alignment guide at each part of a member that is connected to another member. An alignment guide, as used herein, can be anything su...
PUM
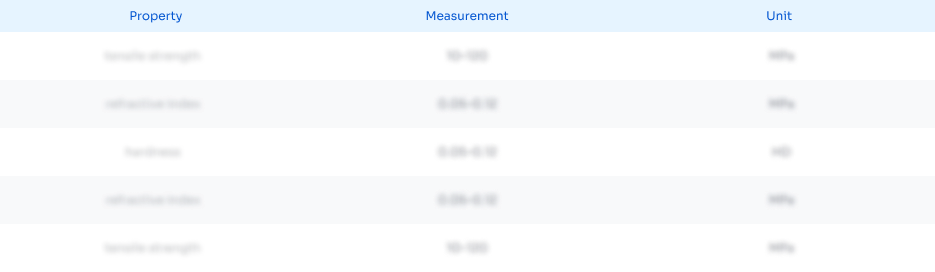
Abstract
Description
Claims
Application Information

- R&D
- Intellectual Property
- Life Sciences
- Materials
- Tech Scout
- Unparalleled Data Quality
- Higher Quality Content
- 60% Fewer Hallucinations
Browse by: Latest US Patents, China's latest patents, Technical Efficacy Thesaurus, Application Domain, Technology Topic, Popular Technical Reports.
© 2025 PatSnap. All rights reserved.Legal|Privacy policy|Modern Slavery Act Transparency Statement|Sitemap|About US| Contact US: help@patsnap.com