Stator iron core of electric motor, manufacturing method thereof, electric motor, and compressor
a technology of electric motors and steel cores, which is applied in the direction of dynamo-electric machines, magnetic circuit shapes/forms/construction, supports/enclosements/casings, etc., can solve the problems of reducing the efficiency of electric motors, reducing the performance of magnetic materials, and difficulty in maintaining a sufficient stiffness
- Summary
- Abstract
- Description
- Claims
- Application Information
AI Technical Summary
Problems solved by technology
Method used
Image
Examples
embodiment 1
[0071] In the following, the first embodiment of the present invention will be explained by referring to the figures.
[0072] FIGS. 1 and 2 show the first embodiment. FIG. 1 is a plan view of a stator of an electric motor, and FIG. 2 is a plan view showing a part of the electric motor and explaining how to wind a coil wire of the stator of the electric motor.
[0073] In FIG. 1, a reference numeral 1 shows a plate-shaped core segment (magnetic pole segment) made of magnetic material, and a reference numeral 9 shows a connection portion (also called as a joint portion) consisting of a concave portion 3a and a convex portion 3b provided to both surfaces of one end of the magnetic pole segment 3 as a connection means. 4 shows the first iron core member in which plural magnetic pole segments 3 are aligned via an end face 3c and an end face 3d of each segment.
[0074] A reference numeral 5 shows the second iron core member in which plural magnetic pole segments 3 are aligned, and the second iro...
embodiment 2
[0082] In the following, the second embodiment of the present invention will be explained referring to the figures.
[0083] FIG. 3 shows a plan view of the stator of the electric motor according to the second embodiment. In FIG. 3, a reference numeral 3 shows a plate-shaped core segment (magnetic pole segment) made of the magnetic material. A reference numeral 9 shows a connection portion constituted by a concave portion 3a and a convex portion 3b provided to both surfaces of one end of the magnetic pole segment 3 as a connection means. 4 shows the first iron core member in which plural magnetic pole segments 3 are aligned via an end face 3c and an end face 3d of each segment.
[0084] A reference numeral 5 shows the second iron core member in which plural magnetic pole segments 3 are aligned, and the second iron core member and the first iron core member are stacked or laminated alternately. The concave portion 3a of a certain magnetic pole segment 3 is engaged with the convex portion 3...
embodiment 4
[0097] In the following, the fourth embodiment of the present invention will be explained referring to the figures.
[0098] FIGS. 5 and 6 show the fourth embodiment. FIG. 5 shows a plan view of a band-shaped stator of the electric motor, and FIG. 6 shows a plan view of a stator of the electric motor formed circularly.
[0099] In FIG. 5, a reference numeral 21 shows a plate-shaped magnetic pole segment (also called as a core segment), and a reference numeral 22 shows a thin connection portion provided to the magnetic pole segment 21. 21a shows a teeth portion of the magnetic pole segment 21, and 22a and 22b show confronting surfaces of the connection portion located at both sides of the thin connection portion 22. 21b and 21c show V-shaped confronting surfaces of end portions, each of which is located at an opposite side to the thin connection portion 2 of the magnetic pole segment 21 placed at far end.
[0100] A method for manufacturing the stator of the electric motor structured as descr...
PUM
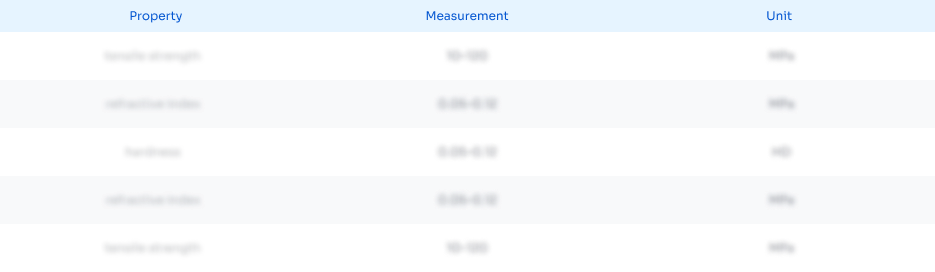
Abstract
Description
Claims
Application Information

- R&D
- Intellectual Property
- Life Sciences
- Materials
- Tech Scout
- Unparalleled Data Quality
- Higher Quality Content
- 60% Fewer Hallucinations
Browse by: Latest US Patents, China's latest patents, Technical Efficacy Thesaurus, Application Domain, Technology Topic, Popular Technical Reports.
© 2025 PatSnap. All rights reserved.Legal|Privacy policy|Modern Slavery Act Transparency Statement|Sitemap|About US| Contact US: help@patsnap.com