Prognostic system and method for an electric coolant pump
a technology of electric coolant and diagnostic system, which is applied in the direction of engine cooling apparatus, positive displacement liquid engine, failure safe, etc., can solve the problems of low coolant flow rate, coolant leakage, overheating of the engine or connected system components, etc., and achieve the effect of facilitating the estimation of a numeric state of health
- Summary
- Abstract
- Description
- Claims
- Application Information
AI Technical Summary
Benefits of technology
Problems solved by technology
Method used
Image
Examples
Embodiment Construction
[0018]Referring to the drawings, wherein like reference numbers refer to like components, FIG. 1 provides a schematic view illustration of a vehicle 10 having a thermal management system 12 that is operable for regulating a temperature of a heat source, shown as an example internal combustion engine (E) 14 having an engine block 14B. In operation, the engine 14 provides engine torque (arrow T14) to a transmission (T) 16 arranged on a driveline 18 along with the engine 14, with the engine 14 and transmission 16 coupled to each other via a hydrodynamic torque converter or an input clutch (not shown). An input member 161 of the transmission 16 is thus supplied with an input torque (arrow TI) that may be selectively assisted as needed by an electric motor (not shown) in optional hybrid embodiments. Within the transmission 16, one or more gear sets and additional clutches (not shown) transfer the input torque (arrow TI) to an output member 160 to thereby deliver an output torque (arrow T...
PUM
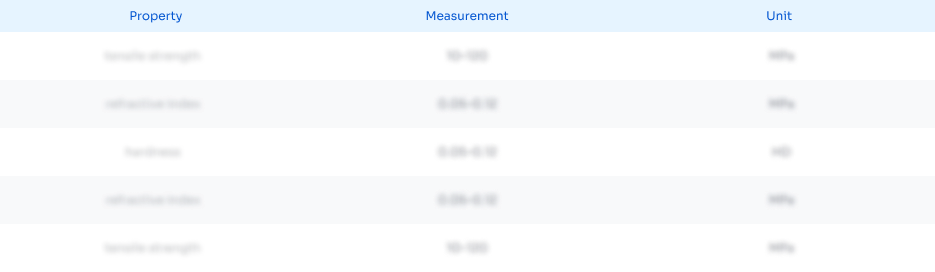
Abstract
Description
Claims
Application Information

- R&D
- Intellectual Property
- Life Sciences
- Materials
- Tech Scout
- Unparalleled Data Quality
- Higher Quality Content
- 60% Fewer Hallucinations
Browse by: Latest US Patents, China's latest patents, Technical Efficacy Thesaurus, Application Domain, Technology Topic, Popular Technical Reports.
© 2025 PatSnap. All rights reserved.Legal|Privacy policy|Modern Slavery Act Transparency Statement|Sitemap|About US| Contact US: help@patsnap.com