Single filament end portion chemical rounding method, brush filament manufacturing method and brush filament manufactured thereof
A manufacturing method and rounding technology, which is applied in the field of toothbrush filaments, can solve the problems of high manufacturing cost and complicated process steps of rounded end monofilaments, and achieve the effect of reducing manufacturing costs and reducing manufacturing costs
- Summary
- Abstract
- Description
- Claims
- Application Information
AI Technical Summary
Problems solved by technology
Method used
Image
Examples
Embodiment 1
[0144] Aqueous sodium hydroxide solution with a concentration of 40% was introduced into a stainless steel shallow-bottomed container. The solution was heated to 120° C. after introduction, wherein the heating temperature was controlled by a glass thermometer. A single PBT monofilament was then placed vertically into the solution to an impregnation depth of 5 mm. After soaking for 10 minutes, the monofilament was taken out, washed with water for 5 minutes, dehydrated and then dried at 50° C. for 10 minutes to obtain the end-rounded monofilament of the present invention.
[0145] The end of the monofilament was observed with a microscope, and the results are shown in FIG. 5 . As can be seen from the comparison of Fig. 5, compared with untreated (Fig. 5a), the monofilament has obtained a good end rounding effect after being processed by the end chemical rounding method of the present invention (Fig. 5b), And there is no smearing that is inevitable with mechanical methods.
Embodiment 2
[0147] Except that the dipping time was changed to 20 minutes, the test and observation were carried out in the same manner as in Example 1. As a result, a monofilament with a round end was obtained, and the photomicrograph of the end is shown in FIG. 6 .
[0148] As can be seen from the comparison of Figure 6, compared with before (Figure 6a) before treatment, the monofilament has obtained a good end rounding effect after being processed by the end chemical rounding method of the present invention (Figure 6b), And there is no smearing that is inevitable with mechanical methods.
Embodiment 3
[0150] In addition to changing the single PBT monofilament to PBT silk cake, changing the concentration of sodium hydroxide aqueous solution to 50%, changing the depth of immersion to 10mm, changing the washing time to 30 minutes, and changing the drying time to 2 hours, with Example 1 also carried out tests and observations. As a result, a silk cake in which the end of each monofilament constituting the silk cake was round was obtained. One of the monofilaments was taken, and the photomicrograph of the end is shown in FIG. 7 .
[0151] As can be seen from the comparison of Fig. 7, compared with untreated (Fig. 7a), the monofilament has obtained a good end rounding effect after being processed by the end chemical rounding method of the present invention (Fig. 7b). , and there is no inevitable tailing of the mechanical method.
PUM
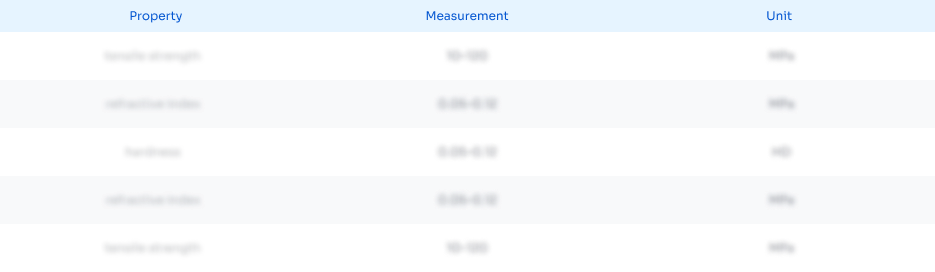
Abstract
Description
Claims
Application Information

- R&D
- Intellectual Property
- Life Sciences
- Materials
- Tech Scout
- Unparalleled Data Quality
- Higher Quality Content
- 60% Fewer Hallucinations
Browse by: Latest US Patents, China's latest patents, Technical Efficacy Thesaurus, Application Domain, Technology Topic, Popular Technical Reports.
© 2025 PatSnap. All rights reserved.Legal|Privacy policy|Modern Slavery Act Transparency Statement|Sitemap|About US| Contact US: help@patsnap.com