Six-coordinate linkage fibre wrapping machine
A technology of fiber winding machine and coordinates, applied in the field of fiber winding machines
- Summary
- Abstract
- Description
- Claims
- Application Information
AI Technical Summary
Problems solved by technology
Method used
Image
Examples
specific Embodiment approach 1
[0006] Specific implementation mode 1: (see Fig. 1-Fig. 6) This embodiment consists of mandrel C-axis rotary motion assembly 1, Z-coordinate linear motion assembly 2, Y-coordinate linear motion assembly 3, and X-coordinate linear motion assembly 4 , B-axis rotary motion assembly 5 and A-axis rotary motion assembly 6, the core mold C-axis rotary motion assembly 1's return transmission axis center line is parallel to the Z coordinate linear motion assembly 2's motion direction; Z coordinate linear motion The trolley 21 of the assembly 2 is set above the Z-coordinate linear motion base 22, the bracket 31 of the Y-coordinate linear motion assembly 3 is fixedly set above the trolley 21, and the X-coordinate linear motion assembly 4 is set on the Y-coordinate linear motion assembly On one side of 3, the B-axis rotary motion assembly 5 is fixedly arranged on one end of the C-axis rotary motion assembly 1 near the mandrel on the shell 42 of the X-coordinate linear motion assembly 4, an...
specific Embodiment approach 2
[0007] Specific embodiment two: (see Fig. 1-Fig. 5) the difference between this embodiment and specific embodiment one is that it also includes connecting plate 7, and described X-coordinate linear motion assembly 4 includes the 3rd servomotor 41, shell 42 , the first lead screw 43, the first lead screw nut 44, the coupling 45, the first lead screw support 46 and the second lead screw support 47, one end of the C-axis rotary motion assembly near the core mold in the inner cavity of the housing 42 is provided There is a first leading screw support 46 and the other end of the casing 42 is fixedly provided with a third servo motor 41, and the middle part of the casing 42 cavity is provided with a second leading screw support 47; one end of the first leading screw 43 is connected to the first Leading screw support 46 is rotationally connected, and the other end of described first leading screw 43 passes second leading screw support 47 and is fixedly connected with the output shaft ...
specific Embodiment approach 3
[0008] Specific embodiment three: (see Fig. 1, Fig. 2, Fig. 6) the difference between this embodiment and specific embodiment one or two is that the Z-coordinate linear motion assembly 2 also includes a fifth servo motor 27 and a rack 28 The upper part of the two side walls of the Z-coordinate linear motion base 22 is respectively provided with a No. 1 guide rail 23 and a No. 2 guide rail 24, and a No. 1 guide groove matching with the No. 25 and No. 2 guide groove 26; rack 28 is fixedly arranged on the outer surface of Z coordinate linear motion base 22 one side, the output gear of the 5th servo motor 27 meshes with rack 28 and servo motor 27 is fixed on the dolly 21. Other compositions and connections are the same as those in Embodiment 1 or Embodiment 2.
PUM
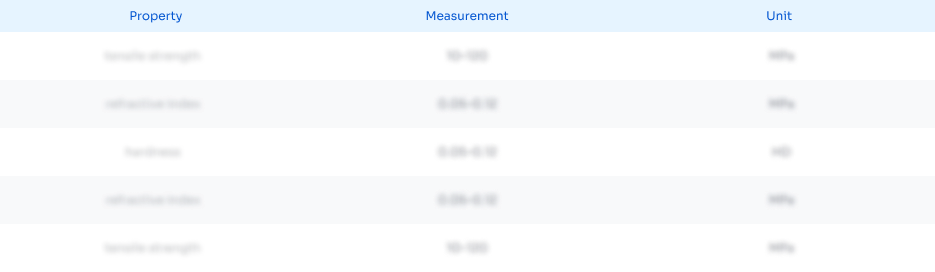
Abstract
Description
Claims
Application Information

- Generate Ideas
- Intellectual Property
- Life Sciences
- Materials
- Tech Scout
- Unparalleled Data Quality
- Higher Quality Content
- 60% Fewer Hallucinations
Browse by: Latest US Patents, China's latest patents, Technical Efficacy Thesaurus, Application Domain, Technology Topic, Popular Technical Reports.
© 2025 PatSnap. All rights reserved.Legal|Privacy policy|Modern Slavery Act Transparency Statement|Sitemap|About US| Contact US: help@patsnap.com