Capacitance type sound sensor in micro mechanical and electrical structure
A micro-electromechanical structure, sound sensor technology, applied in the direction of electrostatic sensors, sensors, sensor types, etc., can solve the problems of stray signal reliability, unstable diaphragm sensitivity, etc., achieve stable and reliable performance, and suppress fluctuation noise.
- Summary
- Abstract
- Description
- Claims
- Application Information
AI Technical Summary
Problems solved by technology
Method used
Image
Examples
Embodiment Construction
[0019] We can obtain capacitive micro-electromechanical structure sound sensors with good sound performance and good practicability from different ways. First, we release the stress in the diaphragm by forming corrugations on it, because the silicon-based diaphragm with a shallow corrugated structure can release its internal stress during the manufacturing process, thereby improving the mechanical sensitivity of the diaphragm and reducing its instability. Compared with the traditional flat diaphragm, the shallow corrugated diaphragm has higher sensitivity, especially for the silicon-based diaphragm which is prone to high residual stress.
[0020] Please refer to Figure 2 to Figure 4 The edge of the suspended shallow corrugated diaphragm 11 of the capacitive MEMS sound sensor according to the first embodiment of the present invention is fixed at a position on the substrate 12, which is essentially formed as a tuning fork structure. The connection terminal 24 is used to connec...
PUM
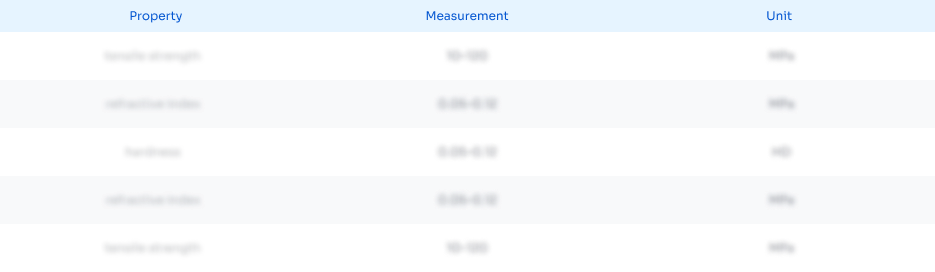
Abstract
Description
Claims
Application Information

- R&D Engineer
- R&D Manager
- IP Professional
- Industry Leading Data Capabilities
- Powerful AI technology
- Patent DNA Extraction
Browse by: Latest US Patents, China's latest patents, Technical Efficacy Thesaurus, Application Domain, Technology Topic, Popular Technical Reports.
© 2024 PatSnap. All rights reserved.Legal|Privacy policy|Modern Slavery Act Transparency Statement|Sitemap|About US| Contact US: help@patsnap.com