Method of error compensation in a coordinate measuring machine
A technology for measuring value and coordinate positioning, which is applied to measuring devices, mechanical measuring devices, instruments, etc., and can solve the problems of time-consuming and complicated calibration.
- Summary
- Abstract
- Description
- Claims
- Application Information
AI Technical Summary
Problems solved by technology
Method used
Image
Examples
Embodiment Construction
[0044] figure 1 Shown is the articulating probe mounted on a CMM. The coordinate measuring machine 10 includes a platform 12 on which a workpiece can be placed and an arm 14 movable in X, Y and Z directions relative to the platform 12 . An articulated probe 16 is mounted on the arm 14 of the coordinate measuring machine (CMM). The articulating probe head 16 allows a workpiece measurement probe 18 mounted thereon to rotate about two substantially perpendicular axes A1 and A2.
[0045]The robotic arm 14 is thus movable in the X, Y and Z directions by the X, Y and Z drives (not shown) of the CMM. Scale means (not shown) on X, Y and Z indicate the immediate coordinates of where the arm 14 is located. A rotary drive (not shown) located in the articulated probe enables movement of the probe around the two axes of rotation A1 and A2. This motion is measured by a rotary scale (not shown) located within the articulating probe 16 . The signal from the probe 18 indicative of deflect...
PUM
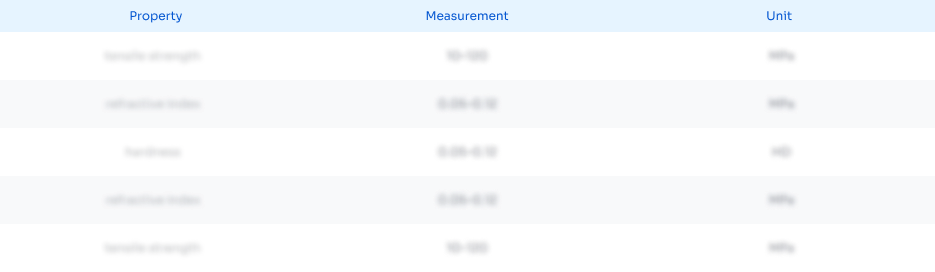
Abstract
Description
Claims
Application Information

- Generate Ideas
- Intellectual Property
- Life Sciences
- Materials
- Tech Scout
- Unparalleled Data Quality
- Higher Quality Content
- 60% Fewer Hallucinations
Browse by: Latest US Patents, China's latest patents, Technical Efficacy Thesaurus, Application Domain, Technology Topic, Popular Technical Reports.
© 2025 PatSnap. All rights reserved.Legal|Privacy policy|Modern Slavery Act Transparency Statement|Sitemap|About US| Contact US: help@patsnap.com