Three freedom degrees decoupling sphere parallel mechanism
A degree of freedom and parallel technology, applied in the field of mechanics, to achieve the effect of increasing the rotary working space, precise control and calibration, and facilitating industrial implementation and application
- Summary
- Abstract
- Description
- Claims
- Application Information
AI Technical Summary
Problems solved by technology
Method used
Image
Examples
Embodiment Construction
[0016] The three-degree-of-freedom decoupling parallel mechanism (hereinafter referred to as the parallel mechanism with a continuously rotating platform described in the present invention, see figure 1 ), including a base 1 and a moving platform 4, and a rotary motion branch chain 2 and two moving motion branch chains 3 and 3' with the same structure that are respectively fixed between the base 1 and the moving platform 4 and are perpendicular to each other; The rotary kinematic branch chain 2 described (see figure 2 ) includes the machine base rotary pair 21 mechanically connected in turn, the machine base Hooke hinge 23, the moving pair 25 and the platform Hooke hinge 27; The center of the hinge 23 intersects and is always perpendicular to a rotation axis of the Hooke hinge 23 of the base; Fixedly connected, its centerline passes through the center of the base Hooke hinge 23 and the platform Hooke hinge 27 respectively; The axis is parallel to the axis of the base rotary...
PUM
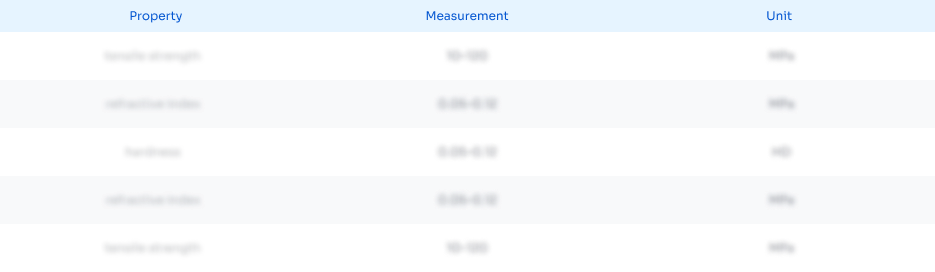
Abstract
Description
Claims
Application Information

- Generate Ideas
- Intellectual Property
- Life Sciences
- Materials
- Tech Scout
- Unparalleled Data Quality
- Higher Quality Content
- 60% Fewer Hallucinations
Browse by: Latest US Patents, China's latest patents, Technical Efficacy Thesaurus, Application Domain, Technology Topic, Popular Technical Reports.
© 2025 PatSnap. All rights reserved.Legal|Privacy policy|Modern Slavery Act Transparency Statement|Sitemap|About US| Contact US: help@patsnap.com