Light composite external wall panel and manufacturing method thereof
A technology for composite exterior wall panels and manufacturing methods, which is applied in the field of building materials, can solve the problems of not being able to meet market demands, and there are not many types of exterior wall panels, and achieve the effect of practical manufacturing methods and high work efficiency
- Summary
- Abstract
- Description
- Claims
- Application Information
AI Technical Summary
Problems solved by technology
Method used
Image
Examples
Embodiment 1
[0038] Such as figure 1 and figure 2 As shown, a kind of lightweight composite exterior wall panel provided by the present invention is composed of fiber-reinforced cement slab 2 and load-bearing layer 1. The load-bearing layer 1 is a light aggregate concrete layer reinforced by steel mesh 3. The load-bearing layer 1 Fiber-reinforced cement slabs 2 are composited on both sides of the wall, and a cavity surrounded by lightweight aggregate concrete is left in the bearing layer 1. The cavity is filled with insulation materials 4. The middle part of this composite exterior wall panel is a five-layer structure : Fiber-reinforced cement slab 2+loading layer 1 (built-in steel mesh 3)+insulation material 4+loading layer 1 (built-in steel mesh 3)+fiber-reinforced cement slab 2, and its two ends are three-layer structure: Reinforced cement slab 2 + load-bearing layer 1 (built-in steel mesh 3 ) + fiber-reinforced cement slab 2, the two ends of the load-bearing layer 1 are set as tenon ...
Embodiment 2
[0041] Such as image 3 and Figure 4 As shown, a kind of lightweight composite exterior wall panel provided by the present invention is composed of fiber-reinforced cement slab 2 and load-bearing layer 1. The load-bearing layer 1 is a light aggregate concrete layer reinforced by steel mesh 3. The load-bearing layer 1 Fiber-reinforced cement slabs 2 are compounded on both sides of the bearing layer 1, and the two ends of the bearing layer 1 are set as tenons and tenons, which is convenient for assembly.
[0042] The concrete for making the load-bearing layer 1 is a lightweight high-strength concrete composed of cement, sand and light aggregate. The light aggregate used in the concrete is polyphenylene particle light aggregate. The cement used is preferably sulphoaluminate cement. Ordinary Portland cement can also be used, and the steel mesh 3 used is a double-layer steel mesh supported by steel bars.
Embodiment 3
[0044] A method for manufacturing a lightweight composite exterior wall panel as in Embodiment 1, comprising the following manufacturing process:
[0045] A. Place the prefabricated fiber-reinforced cement slabs 2 in parallel on both sides in each cavity of the wallboard molding machine;
[0046] B. Place the prefabricated double-layer reinforced mesh 3 supported by steel bars between two cement slabs 2, and pre-clamp the insulation material 4 between the double-layer reinforced mesh 3;
[0047] C. Pour light aggregate concrete between the two cement slabs 2 and between the cement slab 2 and the insulation material 4 to bury the reinforcement mesh 3, and at the same time, vibrate properly so that the light aggregate concrete fills the cavity in the cavity;
[0048] D. Stand for curing for a certain period of time, demoulding and stacking after the light aggregate concrete hardens.
PUM
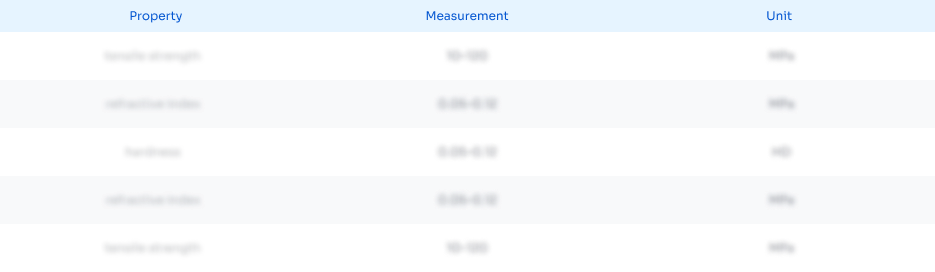
Abstract
Description
Claims
Application Information

- R&D
- Intellectual Property
- Life Sciences
- Materials
- Tech Scout
- Unparalleled Data Quality
- Higher Quality Content
- 60% Fewer Hallucinations
Browse by: Latest US Patents, China's latest patents, Technical Efficacy Thesaurus, Application Domain, Technology Topic, Popular Technical Reports.
© 2025 PatSnap. All rights reserved.Legal|Privacy policy|Modern Slavery Act Transparency Statement|Sitemap|About US| Contact US: help@patsnap.com