Hand robot
A manipulator and gripping force technology, applied in manipulators, program-controlled manipulators, chucks, etc., can solve the problems of increased manufacturing cost of manipulators, high price of multi-axis force sensor devices, and difficulty in realizing gripping force control.
- Summary
- Abstract
- Description
- Claims
- Application Information
AI Technical Summary
Problems solved by technology
Method used
Image
Examples
Embodiment Construction
[0029] The above and other objects, features, and advantages of the present invention will be clarified by the following description of the preferred embodiments with reference to the accompanying drawings.
[0030] Hereinafter, embodiments of the present invention will be described in detail with reference to the drawings. In the drawings, the same or similar structural elements are denoted by common reference signs.
[0031] With reference to the accompanying drawings, figure 1 It is a functional block diagram showing the basic structure of the gripping robot of the present invention. like figure 1As shown, the gripping robot 10 of the present invention includes a plurality of finger mechanisms 18 each having a finger joint 12 , a driver 14 for driving the finger joint 12 , and a link 16 supported on the finger joint 12 and operated by the driving force of the driver 14 . The holding type manipulator 10 also has: the action control part 20 that can control the respective ...
PUM
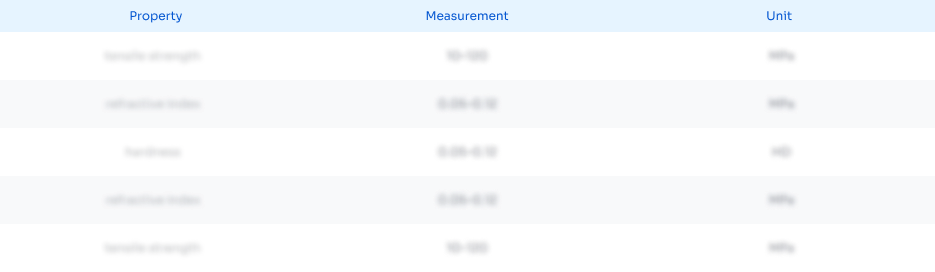
Abstract
Description
Claims
Application Information

- R&D Engineer
- R&D Manager
- IP Professional
- Industry Leading Data Capabilities
- Powerful AI technology
- Patent DNA Extraction
Browse by: Latest US Patents, China's latest patents, Technical Efficacy Thesaurus, Application Domain, Technology Topic, Popular Technical Reports.
© 2024 PatSnap. All rights reserved.Legal|Privacy policy|Modern Slavery Act Transparency Statement|Sitemap|About US| Contact US: help@patsnap.com