Method for manufacturing motor stator
A manufacturing method and technology for motor stators, which are applied in the manufacture of motor generators, stator/rotor bodies, electrical components, etc., can solve problems such as difficulty in winding operation and motor constraints, and achieve the effect of convenient winding operation and improved efficiency.
- Summary
- Abstract
- Description
- Claims
- Application Information
AI Technical Summary
Problems solved by technology
Method used
Image
Examples
Embodiment Construction
[0017] Embodiments of the present invention will be described in detail below with reference to the accompanying drawings.
[0018] The motor stator 50 of the present invention is made through the following process, namely: tooth forming process ( figure 2 a), in this process, several teeth 54 need to be formed, and these teeth 54 are arranged along the circumferential direction of the rotor 60 while retaining certain slots 52; the yoke forming process ( figure 2 b), in this process, it is necessary to form a strip-shaped magnetic yoke 56 for connecting the above-mentioned several teeth 54; the winding process ( figure 2 c), in this process, coils 59 need to be wound on bobbins 58 that can be respectively inserted into the outsides of the above-mentioned teeth 54; the assembly process ( figure 2 d), in this process, it is necessary to insert the bobbins 58 wound with the above-mentioned coils 59 between the teeth 54 respectively, and then connect the above-mentioned teeth...
PUM
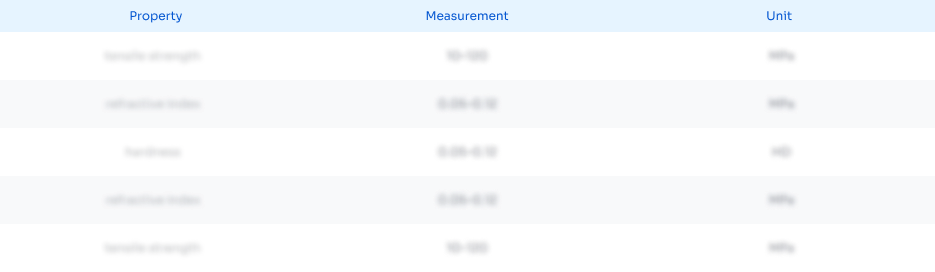
Abstract
Description
Claims
Application Information

- R&D Engineer
- R&D Manager
- IP Professional
- Industry Leading Data Capabilities
- Powerful AI technology
- Patent DNA Extraction
Browse by: Latest US Patents, China's latest patents, Technical Efficacy Thesaurus, Application Domain, Technology Topic, Popular Technical Reports.
© 2024 PatSnap. All rights reserved.Legal|Privacy policy|Modern Slavery Act Transparency Statement|Sitemap|About US| Contact US: help@patsnap.com