Curve swing head supersonic mciro motor composed of multiple piezoelectric lamination pile transducer
A transducer and piezoelectric sheet technology, which is applied in the field of ultrasonic motor structure design, can solve the problem that the resonance frequency of the two signals of the motor is not degenerate, the upper and lower positions of the two piezoelectric sheets are different, and the thickness of the piezoelectric sheet cannot be too thin and other problems, to achieve the effect of excellent operating performance, degeneracy of resonance frequency, and promotion of miniaturization and industrialization
- Summary
- Abstract
- Description
- Claims
- Application Information
AI Technical Summary
Problems solved by technology
Method used
Image
Examples
Embodiment 1
[0036] The present invention has designed the first embodiment of the piezoelectric ultrasonic motor. In this embodiment, in addition to using multiple groups of piezoelectric lamination stack transducers as piezoelectric elements, other structures adopt the patented ultrasonic motor of the applicant. Similar structures, such as Figure 11 As shown, the motor is composed of a rotor 111 , a stator 112 and a central shaft 113 . Wherein, the stator 112 is composed of an upper matching block 1121 , a stack of multilayer piezoelectric ceramic laminations 1122 , electrode lead-out sheets 1123 , and a lower matching block 1124 . The rotor 111 is composed of a preload nut 1111 , a fixed bracket 1112 , a gear 1113 , a transition piece A1114 , a transition piece B1115 , a motor rotor 1116 and a preload spring 1117 .
[0037]The inner hole of the upper matching block 1121 is a threaded hole 11211, and it is connected with the screw part 1131 of the central shaft 113, and the screwing be...
Embodiment 2
[0052] The overall structure of the motor in this embodiment is an improvement on the structure of Embodiment 1, as Figure 12 As shown, the motor is composed of a rotor 121, a stator 122, and a central shaft 123. Among them, the stator 122 is composed of an upper matching block 1222, a friction material 1221 bonded to the upper end surface of the upper matching block 1222, a multilayer piezoelectric ceramic lamination stack 1223, an electrode lead-out piece 1224, a lower matching block 1225, and a clip with internal threads. Tight nut 1226 is formed. The rotor 121 is made up of a preload nut 1211 , a fixed bracket 1212 , a gear 1213 , a preload spring 1214 and a motor rotor 1215 .
[0053] The friction material 1221 and the upper matching block 1222 are connected together by epoxy resin glue, the inner hole of the upper matching block 1222 is a light hole, and a transition fit is maintained with the central shaft 123, which is realized by the end face of the flange 1232 on t...
PUM
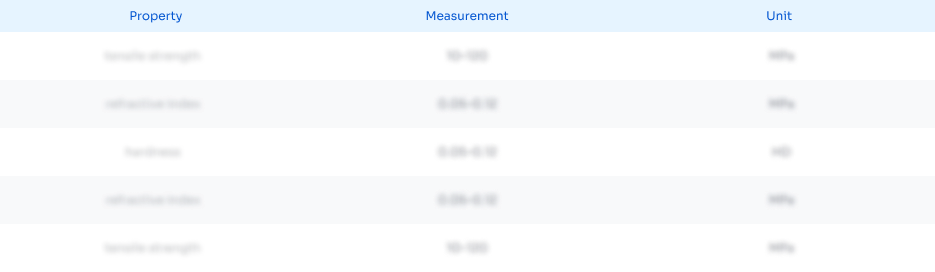
Abstract
Description
Claims
Application Information

- Generate Ideas
- Intellectual Property
- Life Sciences
- Materials
- Tech Scout
- Unparalleled Data Quality
- Higher Quality Content
- 60% Fewer Hallucinations
Browse by: Latest US Patents, China's latest patents, Technical Efficacy Thesaurus, Application Domain, Technology Topic, Popular Technical Reports.
© 2025 PatSnap. All rights reserved.Legal|Privacy policy|Modern Slavery Act Transparency Statement|Sitemap|About US| Contact US: help@patsnap.com