Differential cloth-feed sewing machine
A sewing machine and cloth feeding technology, applied in the direction of cloth feeding mechanism, sewing machine components, program-controlled sewing machines, etc., can solve the problems of lowering sewing quality, lowering productivity, and difficulty in feeding the cloth feeding section, etc., so as to improve sewing quality effect
- Summary
- Abstract
- Description
- Claims
- Application Information
AI Technical Summary
Problems solved by technology
Method used
Image
Examples
Embodiment Construction
[0053] (Overall structure of the embodiment)
[0054] Refer now figure 1 ~ Figure 27 illustrates an embodiment of the present invention. The differential feed sewing machine 10 of this embodiment is a sewing machine that uses a method of setting a difference in the respective feed speeds of the upper and lower cloths to be sewn while folding and sewing. For example, it is used for sleeves and Sewing of large front and rear body, etc.
[0055] In addition, the so-called shirring means that there is a difference in the width of the sewing pitch between the upper cloth and the lower cloth, and increasing the difference (the shirring amount) can make the seam stretchable. Therefore, when sewing the sleeves and the front and back of the body, the amount of stitching on the shoulder side is increased so that it is larger than the underarm side, so that the shoulder side that requires stretchability after sewing can have a margin.
[0056] Here, the direction of the up and down movement...
PUM
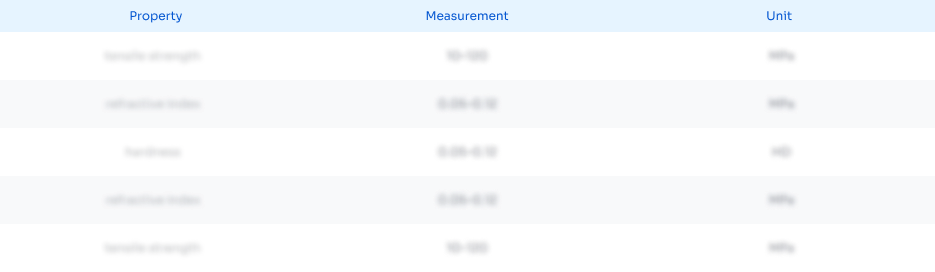
Abstract
Description
Claims
Application Information

- Generate Ideas
- Intellectual Property
- Life Sciences
- Materials
- Tech Scout
- Unparalleled Data Quality
- Higher Quality Content
- 60% Fewer Hallucinations
Browse by: Latest US Patents, China's latest patents, Technical Efficacy Thesaurus, Application Domain, Technology Topic, Popular Technical Reports.
© 2025 PatSnap. All rights reserved.Legal|Privacy policy|Modern Slavery Act Transparency Statement|Sitemap|About US| Contact US: help@patsnap.com