Ceramet material with gradient function for electrolyzing Al
A cermet and gradient function technology, which is applied in the field of gradient function cermet materials for aluminum electrolysis, can solve the problems of metal phase oxidation and selective corrosion, difficult connection of metal guide rods, ceramic phase slag falling off, etc., and achieve good conductivity , change the structure, improve the effect of the environment
- Summary
- Abstract
- Description
- Claims
- Application Information
AI Technical Summary
Problems solved by technology
Method used
Image
Examples
Embodiment 1
[0021] figure 1 described a round rod-shaped NiFe 2 o 4 The gradient structure of / Cu gradient functional cermet material, which is based on NiFe 2 o 4 It is a ceramic phase, and Cu is a metal phase; it is designed as 11 gradient layers, and the taper angle θ between the side gradient layers 1, 2, 3 and the bottom gradient layers 6, 7, and 8 is 45 degrees; the outer layer 4 and the bottom layer The metal phase Cu content of 9 is 5wt%, and the ceramic phase NiFe 2 o 4 The content is 95wt%; the core 5 cermet contains 50wt% Cu, 50wt% NiFe 2 o 4 ; NiFe made of outer layer 4 and bottom layer 9 2 o 4 / Cu cermet layer respectively through 9 NiFe 2 o 4 / Cu gradient cermet layer transition to NiFe in core 5 2 o 4 / Cu cermet, the metal Cu content of adjacent gradient layers differs by 5wt%.
[0022] The side gradient layer of the material is formed by the centrifugal method, the bottom gradient disc is formed by the lamination method, the round rod-shaped core 5 cermet is f...
Embodiment 2
[0024] figure 2 described a plate-shaped NiFe 2 o 4 - Gradient structure of NiO / Cu-Ni gradient functional cermet material, which adopts NiFe doped with 35wt% NiO 2 o 4 It is a ceramic phase, and Cu-Ni alloy is a metal phase; it is designed as 9 gradient layers, and the taper angle θ between the side gradient layers 1, 2, 3 and the bottom gradient layers 6, 7, and 8 is 45 degrees; the outer layer 4 and the ceramic phase NiFe of the bottom layer 9 2 o 4 -NiO content is 90wt%, metal phase Cu-Ni alloy content is 10wt%, wherein Ni content in the alloy is 20wt%; core 5 is NiFe containing 90wt% Ni 2 o 4 -NiO / Ni cermet; NiFe made of outer layer 4 and bottom layer 9 2 o 4 -NiO / Cu-Ni cermet layers are respectively passed through 7 NiFe 2 o 4 -NiO / Cu-Ni gradient cermet layer transition to NiFe in core 5 2 o 4 -NiO / Ni cermet; the metal phase Cu-Ni alloy content of adjacent gradient layers differs by 10wt%; the Ni content in the metal phase alloy differs by 10wt%.
[0025] Th...
Embodiment 3
[0027] image 3 described a goblet NiFe 2 o 4 -Gradient structure of NiO / Cu-Ni gradient functional cermet material, the cup body 8 is NiFe 2 o 4 -NiO / Cu-Ni cermet material, wherein the ceramic phase is NiFe doped with 35wt% NiO 2 o 4 ; The metal phase is a Cu-Ni alloy containing 15wt% Ni, and the metal phase content is 10wt%; the composition is gradiently changed along the axial direction of NiFe 2 o 4 -NiO / Ni gradient functional cermet connects the conductive rod 1 to the cup body 8; NiFe 2 o 4 -NiO / Ni gradient functional cermet designed as 9 gradient layers; bottom layer 7 ceramic phases NiFe2 o 4 - The content of NiO is 90 wt%; the content of metallic phase Ni is 10 wt%; the ceramic phase NiFe of the top layer 2 2 o 4 -The content of NiO is 10wt%; the content of Ni in the metal phase is 90wt%; 2 o 4 - The NiO / Ni gradient cermet layer transitions to the top 2 cermet layer, and the Ni contents of the metal phases of adjacent gradient layers differ by 10 wt%.
[0...
PUM
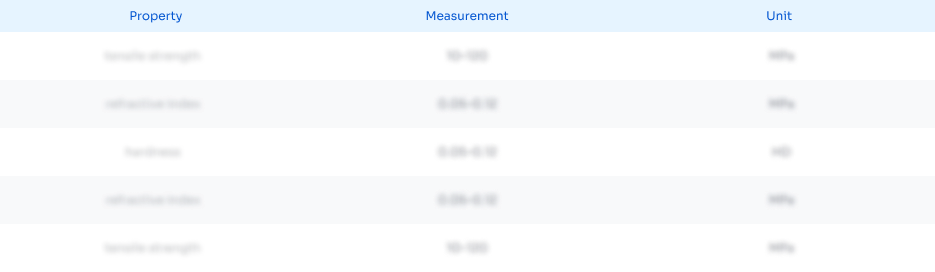
Abstract
Description
Claims
Application Information

- R&D
- Intellectual Property
- Life Sciences
- Materials
- Tech Scout
- Unparalleled Data Quality
- Higher Quality Content
- 60% Fewer Hallucinations
Browse by: Latest US Patents, China's latest patents, Technical Efficacy Thesaurus, Application Domain, Technology Topic, Popular Technical Reports.
© 2025 PatSnap. All rights reserved.Legal|Privacy policy|Modern Slavery Act Transparency Statement|Sitemap|About US| Contact US: help@patsnap.com