Metal filmtype pulse output type steel body elastic micro variable sensor and its measuring method
A technology of pulse output and metal film, applied in the direction of electric/magnetic solid deformation measurement, measuring device, electromagnetic measuring device, etc., can solve the problems affecting the detection accuracy and range, limited mechanical elastic life, complicated bonding process, etc., to achieve convenient Installation, debugging and repair, fast response, good working stability
- Summary
- Abstract
- Description
- Claims
- Application Information
AI Technical Summary
Problems solved by technology
Method used
Image
Examples
Embodiment
[0018] The basic design idea of the steel body elastic micro-variable sensor of metal film pulse output type is as follows figure 1 where: A is the fixed end point of the reference position of the metal film, B is the end point of the force position of the metal film, and I is the metal film connecting A and B. It is assumed that the metal film I has three working states.
[0019] State (1): The reference tension of the metal film I is F 2 In the state of , that is, when the metal film I is at the equilibrium position when the external force is zero, set the natural frequency f of the metal film I 2 equal to the reference frequency f of the static operating point 2 . At this time, when the metal film I is not affected by external force, the corresponding frequency of the mechanical vibration wave is f 2 , also known as the zero reference frequency.
[0020] State (2): The metal film I is at a synthetic tension of F 1 In the state of , that is, the metal film I is under...
PUM
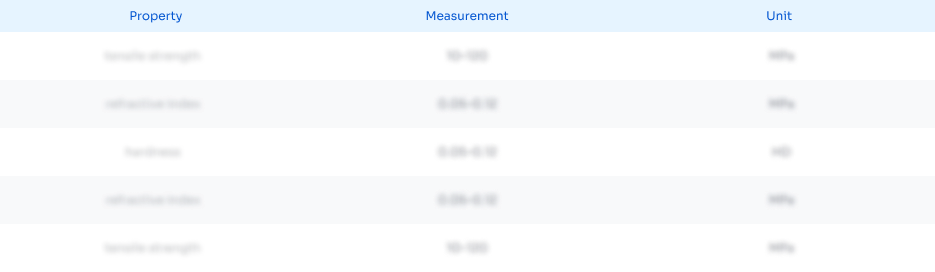
Abstract
Description
Claims
Application Information

- R&D
- Intellectual Property
- Life Sciences
- Materials
- Tech Scout
- Unparalleled Data Quality
- Higher Quality Content
- 60% Fewer Hallucinations
Browse by: Latest US Patents, China's latest patents, Technical Efficacy Thesaurus, Application Domain, Technology Topic, Popular Technical Reports.
© 2025 PatSnap. All rights reserved.Legal|Privacy policy|Modern Slavery Act Transparency Statement|Sitemap|About US| Contact US: help@patsnap.com