Spining technology for viscose rayon continuous spinning machine
A viscose rayon and spinning process technology, applied in the field of spinning process, can solve the problems of high production cost, large floor space, large investment, etc., to reduce production cost and equipment investment cost, improve production efficiency, reduce The effect of a small footprint
- Summary
- Abstract
- Description
- Claims
- Application Information
AI Technical Summary
Problems solved by technology
Method used
Image
Examples
Embodiment Construction
[0010] As shown in the figure, the present invention mainly comprises following technological process: viscose is sprayed from the spinneret hole of spinneret through viscose glue pipe---metering pump---filter---spinneret seat---spinneret, The filaments are solidified in the coagulation bath and formed in the forming tube filled with the coagulation bath. The filaments 1 coming out of the forming tube pass through the acid scraping device, and are formed by the common roller 2 and the small diameter roller 3 with a certain angle from the axis. One end of the formed pair of rollers is spirally wound along its axis, and is wound out from the other end; it is wound on the bobbin 4 through a moving yarn guide to form a bobbin; Oiling and drying, the pair of rollers is composed of 1 common roller 2 and 4 small-diameter rollers 3 in pairs; Two of them bypass the same small-diameter roller 3; each filament 1 has its own metering pump, filter, spinneret holder, spinneret, and moving y...
PUM
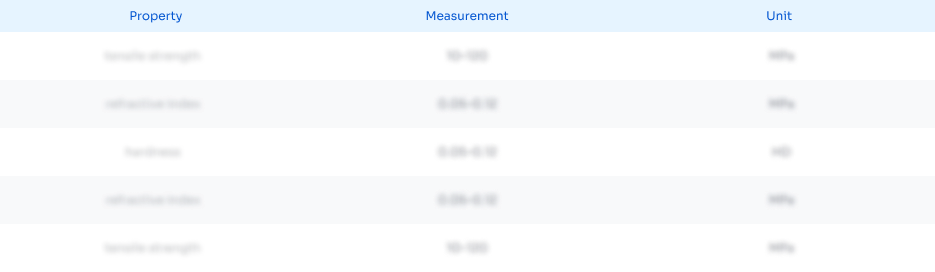
Abstract
Description
Claims
Application Information

- R&D
- Intellectual Property
- Life Sciences
- Materials
- Tech Scout
- Unparalleled Data Quality
- Higher Quality Content
- 60% Fewer Hallucinations
Browse by: Latest US Patents, China's latest patents, Technical Efficacy Thesaurus, Application Domain, Technology Topic, Popular Technical Reports.
© 2025 PatSnap. All rights reserved.Legal|Privacy policy|Modern Slavery Act Transparency Statement|Sitemap|About US| Contact US: help@patsnap.com