Shape memory alloy driven miniature three-leg walking robot
A technology of walking robots and memory alloys, applied in the field of robots, can solve the problems that robots cannot realize turning movements, and achieve the effect of realizing all-round movements
- Summary
- Abstract
- Description
- Claims
- Application Information
AI Technical Summary
Problems solved by technology
Method used
Image
Examples
Embodiment Construction
[0018] The technical solutions of the present invention will be further described below in conjunction with the accompanying drawings and specific embodiments.
[0019] As shown in Fig. 1, the present invention mainly comprises body rotation mechanism, combined offset type SMA driver and walking mechanism.
[0020] The walking mechanism is composed of six symmetrically arranged legs 1 to 6, the six legs are crossed and combined, 1, 3, 5 and 2, 4, 6 are each in a group, and the three legs in each group move synchronously, and the two groups of legs are realized by alternating The actions of lifting, deflecting, and landing are used to realize the forward linear motion of the robot.
[0021] The body rotation mechanism includes two trident supports, an upper trident support 7 and a lower trident support 16, wherein the support 7 is sleeved on the shaft of the support 16, and the two can rotate relatively. Three legs of the same group are respectively connected on each support, ...
PUM
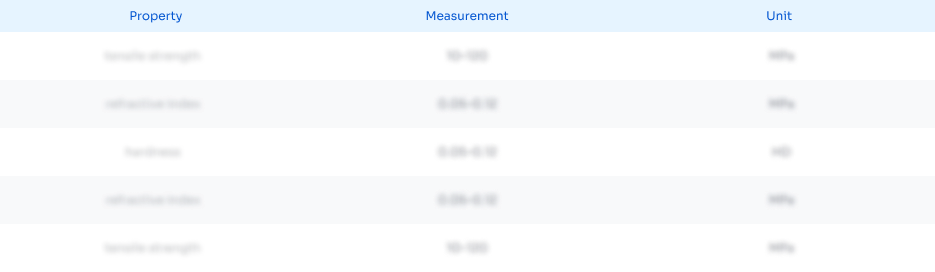
Abstract
Description
Claims
Application Information

- Generate Ideas
- Intellectual Property
- Life Sciences
- Materials
- Tech Scout
- Unparalleled Data Quality
- Higher Quality Content
- 60% Fewer Hallucinations
Browse by: Latest US Patents, China's latest patents, Technical Efficacy Thesaurus, Application Domain, Technology Topic, Popular Technical Reports.
© 2025 PatSnap. All rights reserved.Legal|Privacy policy|Modern Slavery Act Transparency Statement|Sitemap|About US| Contact US: help@patsnap.com