Process and system for preparing low-carbon olefin from methanol or dimethylether
A process method and dimethyl ether technology, which are applied to the process and system field of producing low-carbon olefins from methanol or dimethyl ether, can solve the problems such as the inability to meet the rapid separation of gas and solid, and achieve short gas-solid residence time and processing capacity. Increased, equipment and particle wear is less effective
- Summary
- Abstract
- Description
- Claims
- Application Information
AI Technical Summary
Problems solved by technology
Method used
Image
Examples
Embodiment 1
[0029] The reaction is carried out in a gas-solid co-current down-flow circulating fluidized bed reactor. The feed is dimethyl ether, feed in liquid phase, the catalyst is SAPO34, the temperature of the reactor is 460°C, the temperature of the regenerator is 510°C, the residence time is 10 seconds, the ratio of agent to oil is 30, and the reaction is carried out at 0.01MPa. The conversion rate of dimethyl ether is 99%. In the hydrocarbon products, the proportion of ethylene is 60%, the proportion of propylene is 25%, the proportion of butene is 8%, and the yield of low-carbon olefins is 93%. %.
Embodiment 2
[0031] The reaction is carried out in a gas-solid co-current down-flow circulating fluidized bed reactor. The feed is dimethyl ether in gas phase, the catalyst is SAPO34, the temperature of the reactor is 530°C, the temperature of the regenerator is 650°C, the residence time is 5 seconds, the ratio of agent to oil is 18, and the reaction is carried out under normal pressure. The conversion rate of dimethyl ether is 99%. Among the hydrocarbon products, the proportion of ethylene is 63%, the proportion of propylene is 24%, the proportion of butene is 7%, and the yield of low-carbon olefins is 95%. %.
Embodiment 3
[0033]The reaction is carried out in a gas-solid co-current down-flow circulating fluidized bed reactor. The feed is a mixture of dimethyl ether and water, gas-phase feed, the catalyst is SAPO34, the molar ratio of dimethyl ether and water is 1:0.5, the temperature of the reactor is 650°C, the temperature of the regenerator is 780°C, and the residence time is 0.2 seconds, the ratio of agent to oil is 5, and the reaction is performed at 0.95MPa. The conversion rate of dimethyl ether is 99%. Among the hydrocarbon products, the proportion of ethylene is 62%, propylene is 24%, butene is 7%, and the yield of low carbon olefins is 94%.
PUM
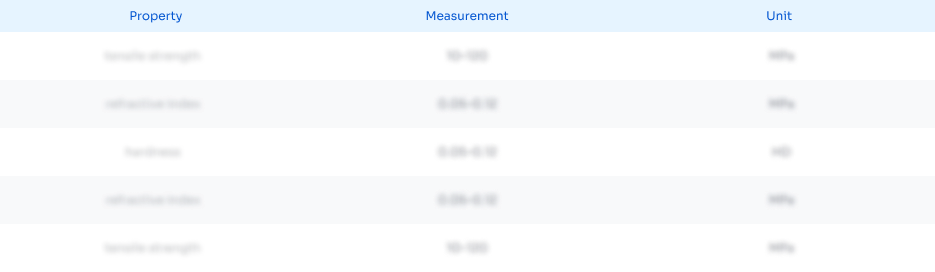
Abstract
Description
Claims
Application Information

- Generate Ideas
- Intellectual Property
- Life Sciences
- Materials
- Tech Scout
- Unparalleled Data Quality
- Higher Quality Content
- 60% Fewer Hallucinations
Browse by: Latest US Patents, China's latest patents, Technical Efficacy Thesaurus, Application Domain, Technology Topic, Popular Technical Reports.
© 2025 PatSnap. All rights reserved.Legal|Privacy policy|Modern Slavery Act Transparency Statement|Sitemap|About US| Contact US: help@patsnap.com