Composite nano high-elastic polyurethane material and its prepn process
A nano-composite material and nano-material technology, applied in the field of high-elastic nano-composite materials, can solve the problems of large fluctuations in the purity and quality of montmorillonite, poor performance reproducibility of industrialized products, etc., and achieve rich varieties, beautiful colors and easy color matching. Effect
- Summary
- Abstract
- Description
- Claims
- Application Information
AI Technical Summary
Problems solved by technology
Method used
Examples
Embodiment 1
[0045] The invention discloses a method for manufacturing a high-elastic nanocomposite material used for laying the ground of a public place.
[0046] The preparation method of component A: based on the total weight of component A, add 40% propylene glycol polyoxypropylene ether with a molecular weight of 2500 and 37% propylene glycol polyoxypropylene ether with a molecular weight of 1000 into the reaction kettle, and heat up to 80°C under stirring. Vacuumize to about -0.1MPa, dehydrate at a temperature of 80°C for 3 hours, cool down to 35°C, slowly add 23% toluene diisocyanate dropwise under stirring, react at 70°C for 2 hours after adding the material, and vacuumize to about -0.1 MPa degassing, cooling to room temperature and discharging for later use.
[0047] The preparation method of component B is: based on the total weight of component B, add 36% glycerol polyoxypropylene ether and 5% inorganic nano-zinc oxide into the reaction kettle, stir, and then add 4% 3,3'- Dichl...
Embodiment 2
[0050] The invention discloses a method for manufacturing a high-elastic plastic nanocomposite material used for laying court ground.
[0051] The preparation method of component A: based on the total weight of component A, add 34% polyether diol with a molecular weight of 2500 and 40% propylene glycol polyoxypropylene ether with a molecular weight of 1000 into the reaction kettle, heat up to 80°C under stirring, pump Vacuum to about -0.1MPa, dehydrate at 80°C for 3 hours, cool down to 35°C, slowly add 26% diisocyanate dropwise under stirring, react at 70°C for 2.5 hours after adding, vacuumize and degas, cool down to room temperature Material spare.
[0052] The preparation method of component B: based on the total weight of component B, add 37% glycerol polyoxypropylene ether, 3% inorganic nano-zinc oxide and 1% nano-silicon oxide into the reaction kettle, stir, and then add 4% 3,3'-dichloro4,4'-diaminodiphenylmethane, 26% talcum powder, 24% chlorinated paraffin oil, 5% iro...
Embodiment 3
[0055] The preparation method of component A: based on the total weight of component A, add 34% polyether diol with a molecular weight of 2500 and 40% propylene glycol polyoxypropylene ether with a molecular weight of 1000 into the reactor, and heat up to 80°C under stirring. Vacuum down to about -0.1MPa, dehydrate at 80°C for 3 hours, cool down to 40°C, slowly add 26% diisocyanate dropwise under stirring, react at 70°C for 3 hours after adding, vacuumize and degas, cool down to room temperature The material is ready for use.
[0056] The preparation method of component B is: based on the total weight of component B, add 36% glycerol polyoxypropylene ether, 1% inorganic nano-silicon oxide and 5% organic hydrotalcite into the reaction kettle, stir, and then add 4% 3,3'-dichloro-4,4'-diaminodiphenylmethane, 27% talc, 24% chlorinated paraffin oil, 2% mixture of tartrazine and phthalocyanine green and 1% antioxidant , heated to 80°C, vacuumed to about -0.1MPa, degassed and dehydr...
PUM
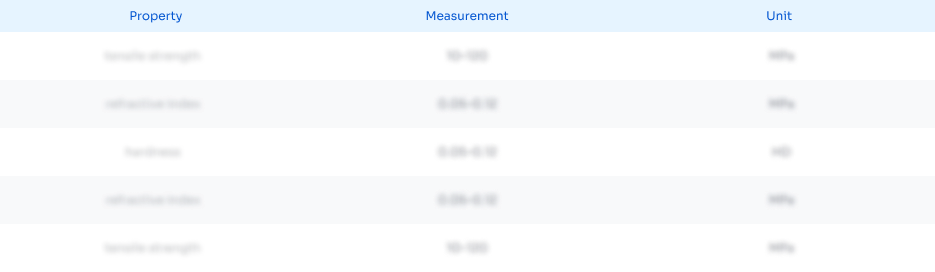
Abstract
Description
Claims
Application Information

- Generate Ideas
- Intellectual Property
- Life Sciences
- Materials
- Tech Scout
- Unparalleled Data Quality
- Higher Quality Content
- 60% Fewer Hallucinations
Browse by: Latest US Patents, China's latest patents, Technical Efficacy Thesaurus, Application Domain, Technology Topic, Popular Technical Reports.
© 2025 PatSnap. All rights reserved.Legal|Privacy policy|Modern Slavery Act Transparency Statement|Sitemap|About US| Contact US: help@patsnap.com