Disc refiner constant pressure pulping method and device
A disc refiner and pressure technology, applied in pulp beating/refining methods, textiles and papermaking, fiber raw material processing, etc., can solve the problem of quality stability and unfavorable quality control parameters, increased working pressure, no consideration, etc. problems, achieve high quality and stability, reduce energy consumption, and reduce the effect of cutting off
- Summary
- Abstract
- Description
- Claims
- Application Information
AI Technical Summary
Problems solved by technology
Method used
Image
Examples
Embodiment
[0018] figure 1 A specific embodiment of the present invention is shown, by figure 1 It can be seen that the disc mill constant pressure beating device of the present invention includes a static disc 1, a moving disc 2, a main shaft 3, an oil cylinder 4, a piston 5, a set screw 6, a limit nut 7, a thrust cylinder 8, etc., the static disc 1 and the moving disc 2 are arranged oppositely, the grinding area is between the two discs, the moving disc 2 is connected to the main shaft 3, the piston 5 is installed in the oil cylinder 4 and positioned outside the thrust cylinder 8, and the thrust cylinder 8 is positioned and sleeved outside the main shaft 4 and connected with the pressure The control components are connected, and the limit nut 7 is sleeved on the thrust cylinder 8 and connected with the thrust cylinder 8 through the set screw 6. One end of the limit nut 7 is connected to the end cover 9 of the oil cylinder 4, and its function is to limit the main shaft. 3 The maximum d...
PUM
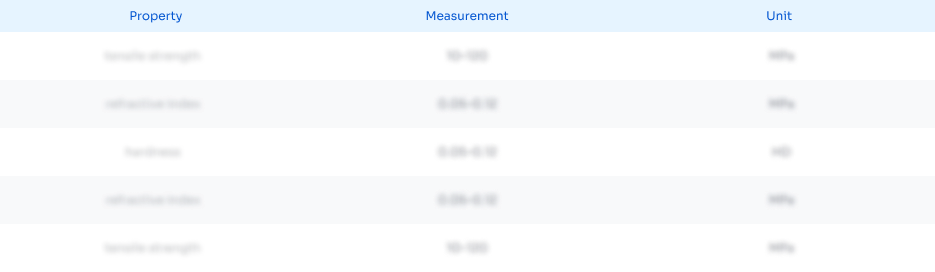
Abstract
Description
Claims
Application Information

- Generate Ideas
- Intellectual Property
- Life Sciences
- Materials
- Tech Scout
- Unparalleled Data Quality
- Higher Quality Content
- 60% Fewer Hallucinations
Browse by: Latest US Patents, China's latest patents, Technical Efficacy Thesaurus, Application Domain, Technology Topic, Popular Technical Reports.
© 2025 PatSnap. All rights reserved.Legal|Privacy policy|Modern Slavery Act Transparency Statement|Sitemap|About US| Contact US: help@patsnap.com