Touch wire-drawing in-die transfer film and preparation method thereof
A wire drawing die and transfer film technology, which is applied in the field of tactile wire drawing in-mold transfer film and its preparation, can solve the problems of in-mold transfer film with shallow texture, complex film structure, and poor adhesion, so as to improve wear resistance , Simplify the membrane structure and save production cost
- Summary
- Abstract
- Description
- Claims
- Application Information
AI Technical Summary
Problems solved by technology
Method used
Image
Examples
Embodiment Construction
[0035] In order to make the objectives, technical solutions and advantages of the present invention clearer, the present invention will be further described in detail below with reference to the accompanying drawings and embodiments. It should be understood that the specific embodiments described herein are only used to explain the present invention, but not to limit the present invention. In addition, the technical features involved in the various embodiments of the present invention described below can be combined with each other as long as they do not conflict with each other.
[0036] like figure 1 As shown, in one embodiment, a tactile in-die transfer film with an antistatic layer 111 is a multi-layered structure that is superimposed layer by layer, and includes, from top to bottom: an antistatic layer 111, a PET layer 112 , UV layer 113 , printing layer 114 , impact resistant layer 115 and adhesive layer 116 .
[0037] The lower surface of the PET layer 112 is provided...
PUM
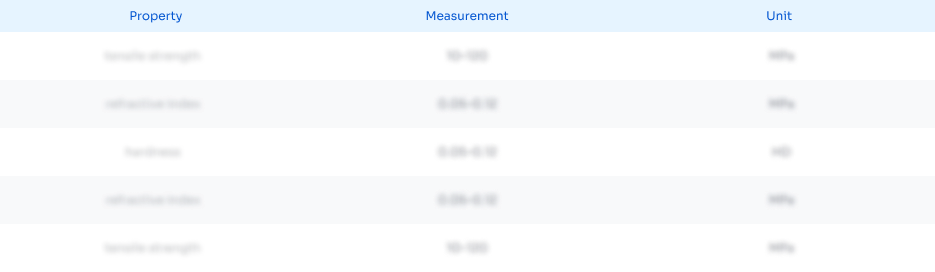
Abstract
Description
Claims
Application Information

- R&D Engineer
- R&D Manager
- IP Professional
- Industry Leading Data Capabilities
- Powerful AI technology
- Patent DNA Extraction
Browse by: Latest US Patents, China's latest patents, Technical Efficacy Thesaurus, Application Domain, Technology Topic, Popular Technical Reports.
© 2024 PatSnap. All rights reserved.Legal|Privacy policy|Modern Slavery Act Transparency Statement|Sitemap|About US| Contact US: help@patsnap.com