Alloy steel resonance girder
An alloy steel and beam technology, applied in the field of alloy steel resonance beams, can solve the problems of loud noise, easy bolt loosening, low assembly efficiency, etc., and achieve the effect of simple connection structure, improving loading and unloading efficiency, and preventing loosening.
- Summary
- Abstract
- Description
- Claims
- Application Information
AI Technical Summary
Problems solved by technology
Method used
Image
Examples
Embodiment
[0035] Example: please refer to Figure 1 to Figure 10 :
[0036] The invention proposes an alloy steel resonance beam, comprising: a vehicle body 1, a resonance beam main body 2 is arranged under the left side of the vehicle body 1; a hammer head 3 is arranged at the front end of the bottom of the resonance beam main body 2; There is a fixed seat 4; the resonance beam main body 2 is provided with positioning frames 5 on the left and right sides of the middle part, and the two positioning frames 5 are distributed in a symmetrical manner; a connecting seat 6 is arranged between the two positioning frames 5, and the top of the connecting seat 6 The vehicle body 1 is connected; the resonance beam main body 2 is provided with a sleeve frame assembly 8; the upper part of the sleeve frame assembly 8 is provided with a counterweight seat 7, and the counterweight seat 7 is connected with the vehicle body 1; The bottom plate 9 is connected at the place, and the connecting bottom plate...
PUM
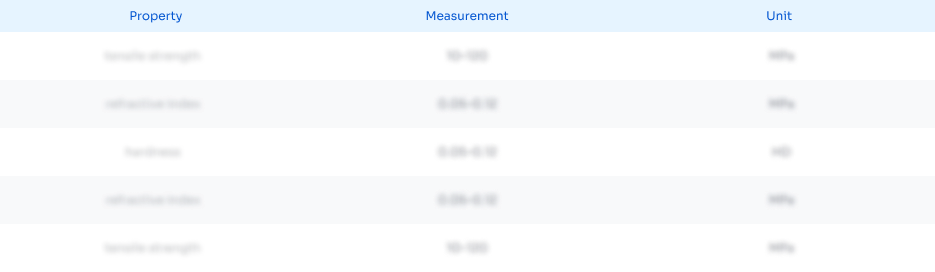
Abstract
Description
Claims
Application Information

- Generate Ideas
- Intellectual Property
- Life Sciences
- Materials
- Tech Scout
- Unparalleled Data Quality
- Higher Quality Content
- 60% Fewer Hallucinations
Browse by: Latest US Patents, China's latest patents, Technical Efficacy Thesaurus, Application Domain, Technology Topic, Popular Technical Reports.
© 2025 PatSnap. All rights reserved.Legal|Privacy policy|Modern Slavery Act Transparency Statement|Sitemap|About US| Contact US: help@patsnap.com