Bionic peristaltic tensegrity robot
A tensioning whole and robot technology, applied in the field of robots, can solve the problems of heavy weight and complex robot structure, and achieve the effects of light weight, simple structure, and low processing and manufacturing costs.
- Summary
- Abstract
- Description
- Claims
- Application Information
AI Technical Summary
Problems solved by technology
Method used
Image
Examples
Embodiment 1
[0031] In a typical embodiment of the present invention, such as figure 1 As shown, the bionic peristaltic tensioning overall robot disclosed in this embodiment is a two-rod four-cable tensioning unit, and the whole unit consists of 1 driving pressing bar 1, 1 arc-shaped elastic pressing bar 2 and 4 ropes (rope 3, rope 4, rope 5, rope 6), the power source for the device to advance is to drive the pressure rod 1, wherein the arc-shaped elastic pressure rod 3 is arc-shaped, and it has a first end and a second end. The pressure rod 1 is arranged along the radial direction of the arc-shaped elastic pressure rod 3. The driving pressure rod 1 also has a first end and a second end. The first end of the driving pressure rod 1 passes through the rope 3, the rope 5 and the curved elastic pressure rod. The first end and the second end of 2 are connected, and the second end of the driving pressure rod 1 is connected with the first end and the second end of the arc elastic pressure rod 2 t...
Embodiment 2
[0040] Such as Figure 6 As shown, this embodiment discloses another bionic peristaltic tensegrity robot, which differs from Embodiment 1 in that no parallelogram is formed between the four ropes, and the length of the two ropes on the left side is greater than that on the right side. The structure of the two ropes is exactly the same as in Embodiment 1, and the movement process and principle of the robot and the robot in Embodiment 1 are also completely the same, so details are not repeated here.
[0041] It is not difficult to understand that in other embodiments, the length of the two ropes on the right side may also be greater than the length of the two ropes on the left side.
PUM
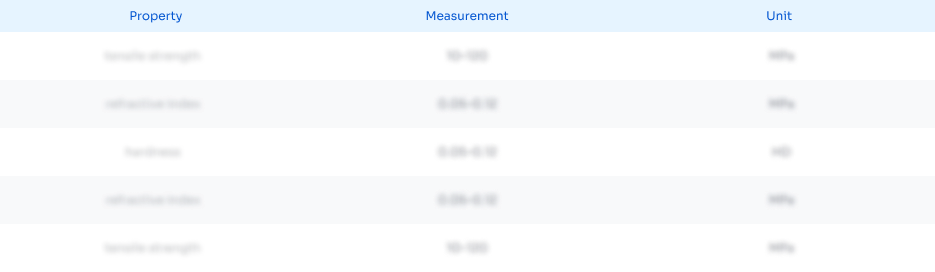
Abstract
Description
Claims
Application Information

- R&D
- Intellectual Property
- Life Sciences
- Materials
- Tech Scout
- Unparalleled Data Quality
- Higher Quality Content
- 60% Fewer Hallucinations
Browse by: Latest US Patents, China's latest patents, Technical Efficacy Thesaurus, Application Domain, Technology Topic, Popular Technical Reports.
© 2025 PatSnap. All rights reserved.Legal|Privacy policy|Modern Slavery Act Transparency Statement|Sitemap|About US| Contact US: help@patsnap.com