End effector for tunnel detection robot, detection robot and control method thereof
A technology of end effectors and robots, which is applied in the direction of program control manipulators, manipulators, manufacturing tools, etc., can solve problems such as harsh working environment, long tunnel distance, affecting detection stability and precision, etc., to improve safety and stability, Improve efficiency and precision, improve the effect of adjustment flexibility
- Summary
- Abstract
- Description
- Claims
- Application Information
AI Technical Summary
Problems solved by technology
Method used
Image
Examples
Embodiment 1
[0043] Such as figure 1 As shown, this embodiment provides an end effector for a tunnel detection robot, including an end effector frame 51, and an ultrasonic radar 52 arranged on the end effector frame 51;
[0044] A plurality of contact switches are arranged on the working surface of the end effector frame 51 .
[0045] In this embodiment, the end effector frame 51 is a rectangular frame, and the four corners of the rectangular frame are provided with contact switches; respectively the first contact switch 53, the second contact switch 54, and the third contact switch 54 and the fourth contact switch 55;
[0046] Specifically, a plurality of contact switches are provided on the working surface of the end effector frame 51, through the cooperation of the plurality of contact switches, the bonding between the end effector and the ultrasonic radar 52 and the detection object is realized. In this implementation, the detection object is The inner wall of the tunnel improves the...
Embodiment 2
[0048] This embodiment provides a method for controlling an end effector for a tunnel inspection robot, using the end effector for a tunnel inspection robot as described in Embodiment 1, including:
[0049] When only one contact switch touches the detection object, the coordinate system is established with the contact point, and the end effector frame 51 rotates around any side where the contact point meets;
[0050] When two adjacent contact switches touch the detection object, a coordinate system is established with the midpoint of the line connecting the two contact points, and the end effector frame 51 rotates around the line connecting the two contact points until three contact switches touch the detection object;
[0051] When two diagonal contact switches touch the detection object, a coordinate system is established with the center of the end effector frame, and the end effector frame 51 rotates around the diagonals of the two contact switches until three contact switches...
Embodiment 3
[0054] This embodiment provides a detection robot, including a robot mobile platform 1, a lift 2, a mechanical arm 3, an extension rod 4, an end effector 5, a laser radar 6 and a gyroscope; the mechanical arm 3 can be set as a six-axis mechanical Arm, the lidar 6 can be set as a 3D lidar.
[0055] The robot mobile platform 1 is equipped with a 3D laser radar and a gyroscope, the elevator 2 is installed above the platform, a six-axis mechanical arm is installed above the elevator 2, and the extension rod 4 is installed at the end of the six-axis mechanical arm. The end effector 5 is installed at the end of the rod 4; the robot is equipped with a server as the control center of the robot, and the control center receives the input of the operator's tunnel detection, and realizes communication with the control systems of each part according to the control logic according to the input data of each part of the system. The control system of each part realizes automatic walking and de...
PUM
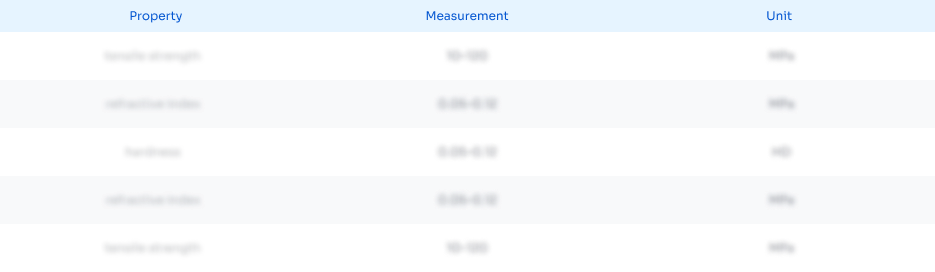
Abstract
Description
Claims
Application Information

- R&D
- Intellectual Property
- Life Sciences
- Materials
- Tech Scout
- Unparalleled Data Quality
- Higher Quality Content
- 60% Fewer Hallucinations
Browse by: Latest US Patents, China's latest patents, Technical Efficacy Thesaurus, Application Domain, Technology Topic, Popular Technical Reports.
© 2025 PatSnap. All rights reserved.Legal|Privacy policy|Modern Slavery Act Transparency Statement|Sitemap|About US| Contact US: help@patsnap.com