Unmanned aerial vehicle thickness measuring system based on electromagnetic ultrasonic technology
An electromagnetic ultrasonic and unmanned aerial vehicle technology, applied in the direction of electromagnetic measuring devices, electric/magnetic thickness measurement, using electromagnetic means, etc., can solve problems that affect the construction progress and generate greater risks, so as to improve coverage and reduce detection costs and artificial risk, the effect of light weight
- Summary
- Abstract
- Description
- Claims
- Application Information
AI Technical Summary
Problems solved by technology
Method used
Image
Examples
specific Embodiment approach 1
[0016] Specific implementation mode one: combine Figure 1 to Figure 3 Describe this embodiment, a kind of UAV thickness measurement system based on electromagnetic ultrasonic technology described in this embodiment, it includes UAV platform 1; This embodiment also includes electromagnetic ultrasonic sensor 5, image transmission module 9, electromagnetic Thick module 10 and first connection assembly; Electromagnetic ultrasonic sensor 5 is installed on the front end of unmanned aerial vehicle platform 1 through described first connection assembly, and image transmission module 9 is installed in the middle part in unmanned aerial vehicle platform 1, and electromagnetic ultrasonic thickness measuring module 10 is mounted on the rear of the unmanned aerial vehicle platform 1.
[0017] In this embodiment, the UAV platform 1 is also provided with a sensor control module; the sensor control module includes a pull-out sensor and a semi-flexible connection follow-up of the sensor. Sem...
specific Embodiment approach 2
[0018] Specific implementation mode two: combination Figure 1 to Figure 3 To illustrate this embodiment, the first connection assembly of an unmanned aerial vehicle thickness measurement system based on electromagnetic ultrasonic technology in this embodiment includes a first connector 4, a slide tube 6, a telescopic rod 7 and a power unit 8; A connector 4 is fixedly installed on the front end of the UAV platform 1, the power unit 8 is fixedly installed on the first connector 4, the electromagnetic ultrasonic sensor 5 is installed on the front end of the slide tube 6, and the rear end of the slide tube 6 passes through the telescopic rod 7 It is connected with the power unit shaft of the power unit 8. Other components and connections are the same as those in the first embodiment.
specific Embodiment approach 3
[0019] Specific implementation mode three: combination Figure 1 to Figure 3 To illustrate this embodiment, a UAV thickness measurement system based on electromagnetic ultrasonic technology described in this embodiment also includes a probe cover 3; superior. Other compositions and connections are the same as those in Embodiment 1 or 2.
PUM
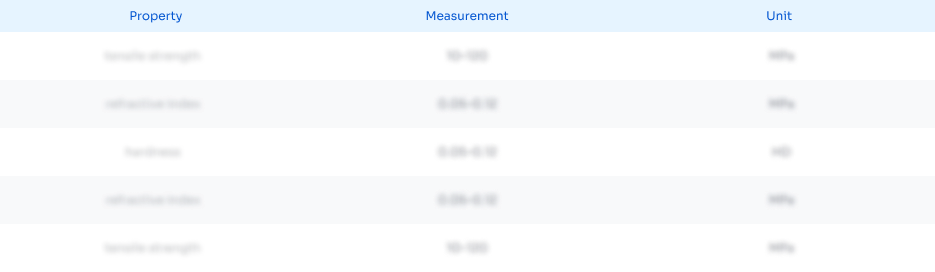
Abstract
Description
Claims
Application Information

- R&D Engineer
- R&D Manager
- IP Professional
- Industry Leading Data Capabilities
- Powerful AI technology
- Patent DNA Extraction
Browse by: Latest US Patents, China's latest patents, Technical Efficacy Thesaurus, Application Domain, Technology Topic, Popular Technical Reports.
© 2024 PatSnap. All rights reserved.Legal|Privacy policy|Modern Slavery Act Transparency Statement|Sitemap|About US| Contact US: help@patsnap.com